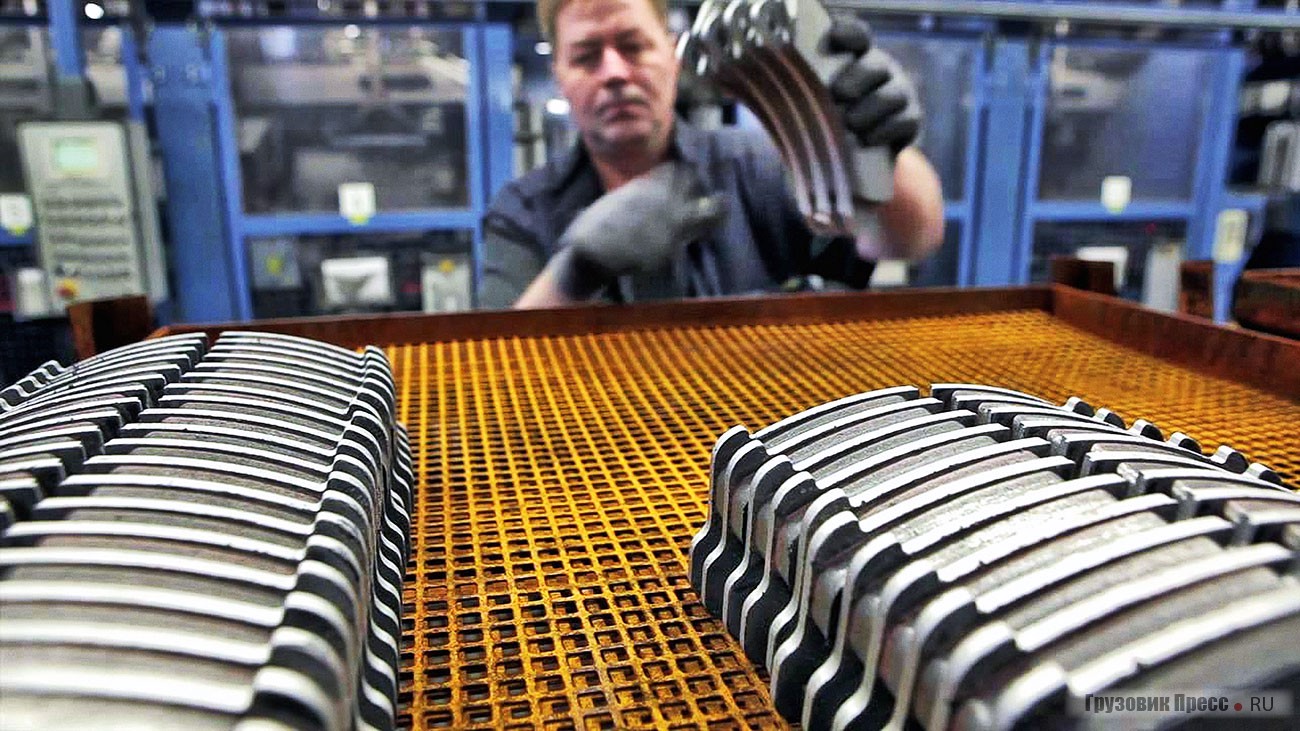
Завод по производству тормозных колодок и накладок TMD Friction Group
Немецкий городок Хамм, расположившийся на северо-западе Германии, почти на границе между Бельгией и Голландией, найдёшь не на всех картах. Он не отмечен на дорожных знаках, а потому добраться до него можно разве что по наводке: доедешь до Дортмунда, а потом бери правее. Но на днях российское представительство компании TMD Friction Group пригласило меня посетить завод по производству тормозных колодок и накладок для тяжёлых грузовиков, который располагается именно в Хамме, и я в полной мере понял значение этого незаметного населённого пункта для всего европейского автопрома.
Всё знать невозможно, а уж тем более о том, колодка какого производителя стоит на том или ином грузовике. Посмотреть, конечно, можно, но это мало что даст. Уверен, что на тягаче DAF вы найдёте колодку DAF, на автомобиле Scania – колодку Scania, на машине Volvo – колодку Volvo и т. д. Но очень высока вероятность, что все они были изготовлены в небольшом немецком городе Хамм.
Важный компонент
TMD Friction Group – это международная компания, так как её 17 заводов расположены по всему миру, на разных континентах, а сама она с 2011 г. входит в японскую корпорацию NISSHINBO. Чтобы представить масштабы производственной деятельности этого производителя, назову всего две цифры: заводы этой группы ежедневно выпускают один миллион тормозных колодок, а оборот её финансовых средств в 2015 г. составил 715 млн евро. Основными заказчиками являются все мировые производители автомобилей и тормозных систем. Ассортимент покрывает 99 % автопарка.
За 135 лет своего существования TMD Friction стала ведущим мировым производителем тормозных колодок и накладок. Причём сфера её влияния очень широкая, она делает тормозные компоненты для спортивных автомобилей, легкового, коммерческого транспорта и для промышленного использования. Все эти годы компания аккуратно отгружала свою продукцию на большинство европейских конвейерных сборочных производств, ничем не определяя своей значимости для автомобильного производства. Подумаешь, один из сотен компонентов! Но очень важный для жизни компонент.
Мы делаем то, что лучше всего умеем…
Завод в Хамме создан в 1961 году. Но знаковым этапом здесь считают 1996 год, когда было запущено поточное производство фрикционных материалов. Текущая мощность завода около 8,5 млн колодок и 4,8 млн накладок в год. Из них на конвейерные производства грузовиков уходит 51 % продукции. В сервисные службы компаний отгружается 47 % компонентов в полном комплекте, упакованные в коробки оригиналы под брендом разных производителей. Они предназначены для гарантийного обслуживания при замене и ремонте тяжёлых машин и автобусов. Отгрузки афтермаркет составляют всего 2 %, но это абсолютно не означает, что этому направлению здесь уделяют меньше внимания, просто основной завод для афтермаркета находится в восточной части Германии, недалеко от города Косвиг.
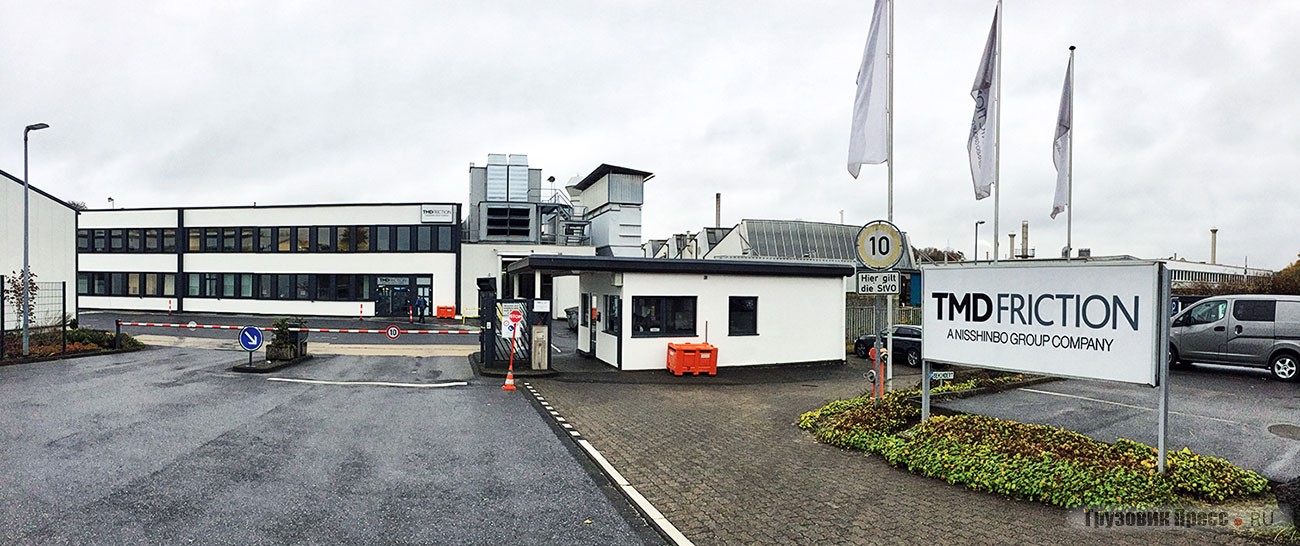
Производство очень наукоёмкое, но всё это невидимая часть. Ежегодно компания инвестирует в исследования и разработку новых составов 30 млн евро, что позволяет ежегодно добавлять 120–150 самых современных и наиболее эффективных артикулов. Европейский Научно-исследовательский центр находится в Ливеркузене, именно там разрабатываются смеси для Европы, там же находится штаб-квартира компании.
На самом заводе никакие исследования не производятся. Поэтому видимая часть включает пять этапов: подготовка смесей, подготовка основания тормозной колодки, прессование, доработка внешних параметров, придание продукту товарного вида. Процесс изготовления накладки примерно такой же, только исключает подготовку основания.

По нашим российским представлениям предприятие небольшое, сейчас на фабрике действует 12 горячих прессов. Но они работают в три смены и останавливаются только один раз в неделю, в воскресенье днём, чтобы не беспокоить жителей, видимо, так положено по местным законам. Хотя я прислушивался – шуму там не много, так что завод никому не мешает. Прессы различаются по количеству станций. Два пресса с шестью станциями отличаются небольшой производительностью, и потому используется на позициях с небольшими объёмами. Другие шесть прессов с 10 станциями перенастраиваются дважды в неделю и используются на средних объёмах производства. А вот главные работники – оставшиеся четыре пресса: два имеют по 19 станций и два по 15 сдвоенных, т. е. фактически два по 30. Эти прессы работают в постоянном режиме, на них не производится перенастройка, они делают одни и те же компоненты.
Для изготовления фрикционных материалов используется около 200 компонентов. Но каждый рецепт составляет не более 20 компонентов. Контроль тотальный, визуальный, компьютерный и лазерный, начиная от стадии составления смеси до отслеживания внешних параметров на выходе детали с конвейера фабрики.
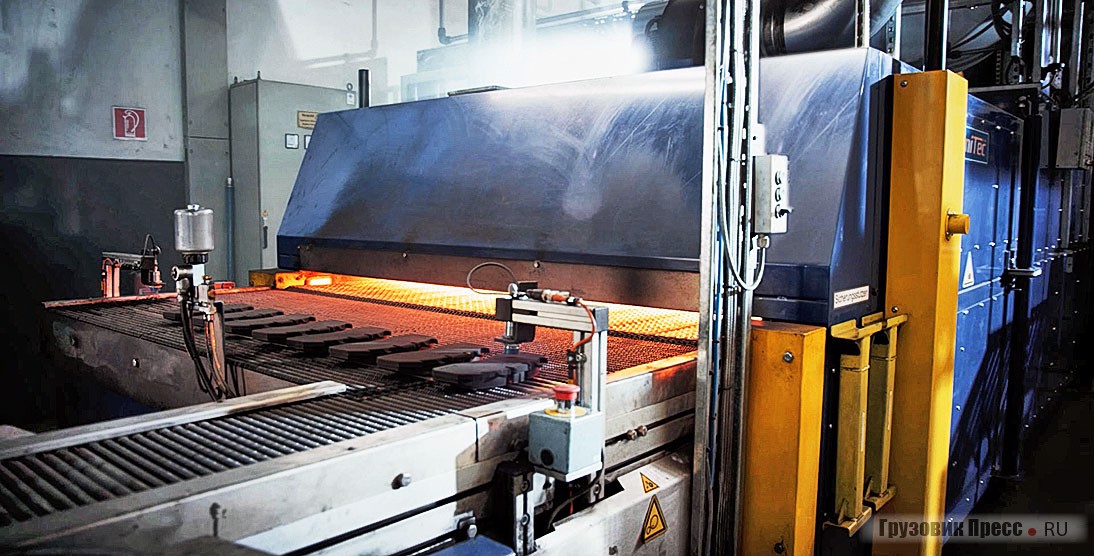
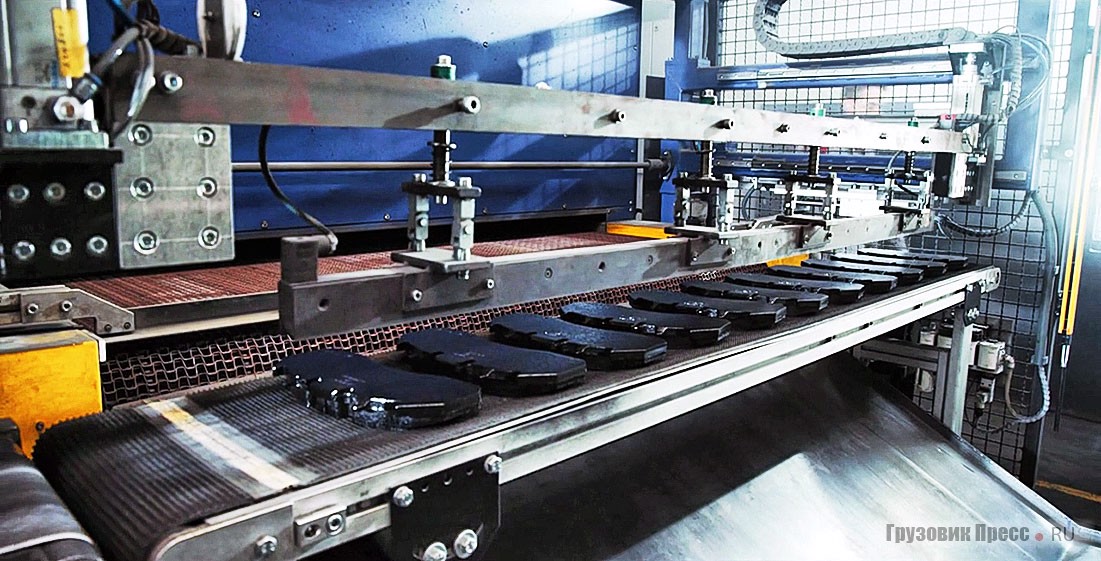
К 2018 году на заводе планируют завершить реструктуризацию и оптимизацию производства от цеха смесей до выхода готовых продуктов, т. е. весь завод.
Не только колодки
Аббревиатура TMD образована от названий торговых марок Textar, Mintex, Don – всё это продукция TMD Friction Group. Около 70 % всех грузовых автомобилей Европы, имеющих барабанные тормозные системы, оснащены тормозными накладками марки Textar. Они поступают на конвейеры таких производителей как DAF, IVECO, MAN, Mercedes-Benz, Neoplan, Renault Trucks, Scania Truck & Bus, Volvo Trucks & Buses, КАМАЗ, Dennis Bus, EvoBus, Irisbus, Arvin Meritor, BPW, Haldex, Kässbohrer, Knorr-Bremse, Perrot / WABCO, Van Hool, Warstein Achsen.
Знаете ли вы, что коммерческие автомобили таких брендов как Volvo, Renault, DAF, Scania на 100 % оснащаются колодками и накладками Textar. Производитель осей BPW – почти на 100 % комплектуется продукцией TMD. Примерно половина машин MAN и 100 % IVECO выходит за ворота сборочных цехов с тормозными накладками TMD. Производитель тормозных систем Meritor использует колодки TMD в 95 % своей продукции, а Knorr-Bremse и WABCO – в 45 %.
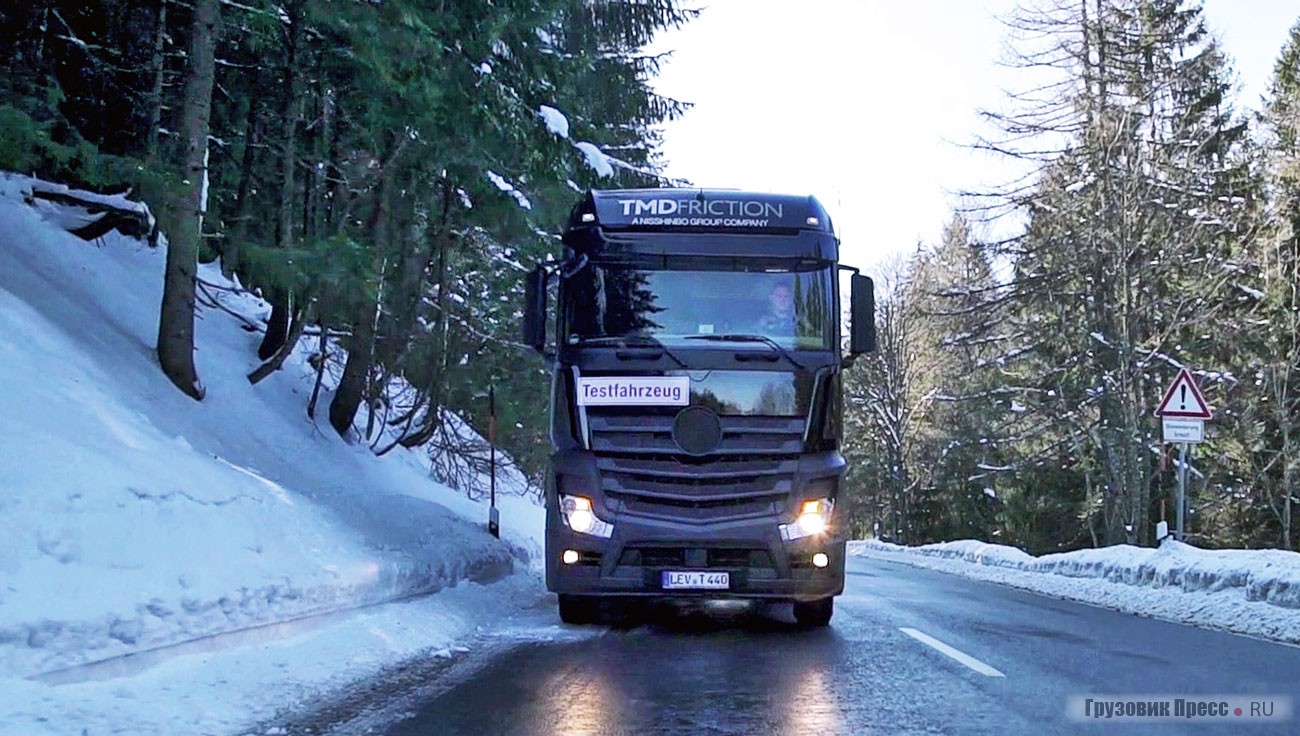
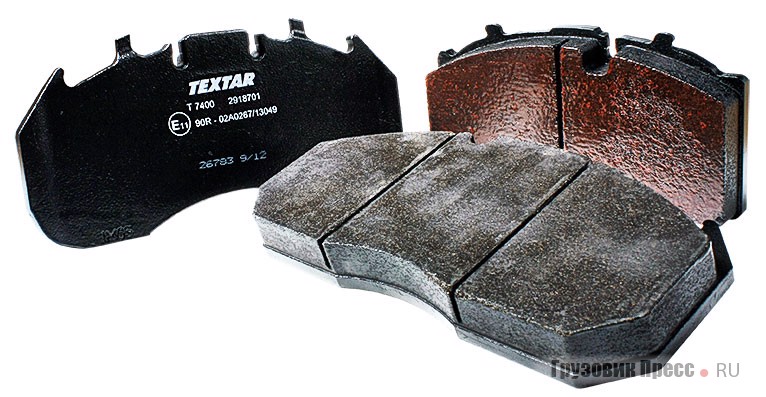
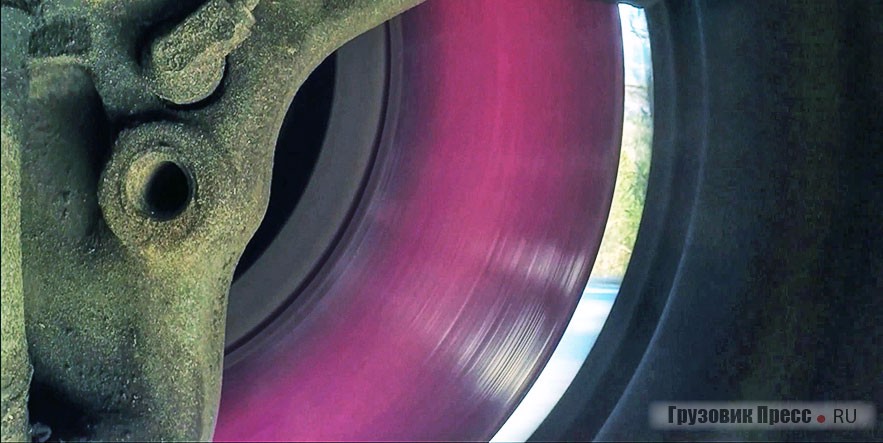
Кстати, ассортимент продукции группы включает не только накладки и колодки для барабанных и дисковых тормозов, компания выпускает специальные смазки, очистители и инструменты для обслуживания элементов тормозной системы легковых и коммерческих автомобилей. Разумеется, в производстве фрикционной и другой продукции компания использует сырьё только высочайшего качества. Это позволяет соблюсти жёсткие стандарты качества и сохранять лидирующие позиции в среде конкурентов.
Несколько историй одного изобретения
- Случайная встреча Уильяма Фентона и Уолтера Уилсона Коббетта в 1878 г. привела к основанию компании Walter Willson Cobbett Ltd, ставшей предшественницей BBA Group. Коббетт изобрёл и запустил в производство принципиально новый тип цельнотканного ремня для машин, создав на его основе фрикционный материал, позволявший полностью останавливать автомобили и другие транспортные средства. В 1910 г. Коббетт поставлял 400 тыс. футов фрикционной ленты в неделю для самого знаменитого автомобиля 20-го века – Ford Model T.
- В 1967 г. Лондонский метрополитен выбрал в качестве поставщика тормозных систем компанию Transport Brakes Ltd. Это сотрудничество продолжается и по сей день с изделиями Cosid от TMD Friction.
- Появление углекерамических дисковых тормозов в 2000 г. позволило компании TMD Friction разработать первые тормозные колодки для этого оборудования. Компания TMD Friction была приглашена к разработке и производству фрикционных материалов для самого быстрого автомобиля – Bugatti Veyron.