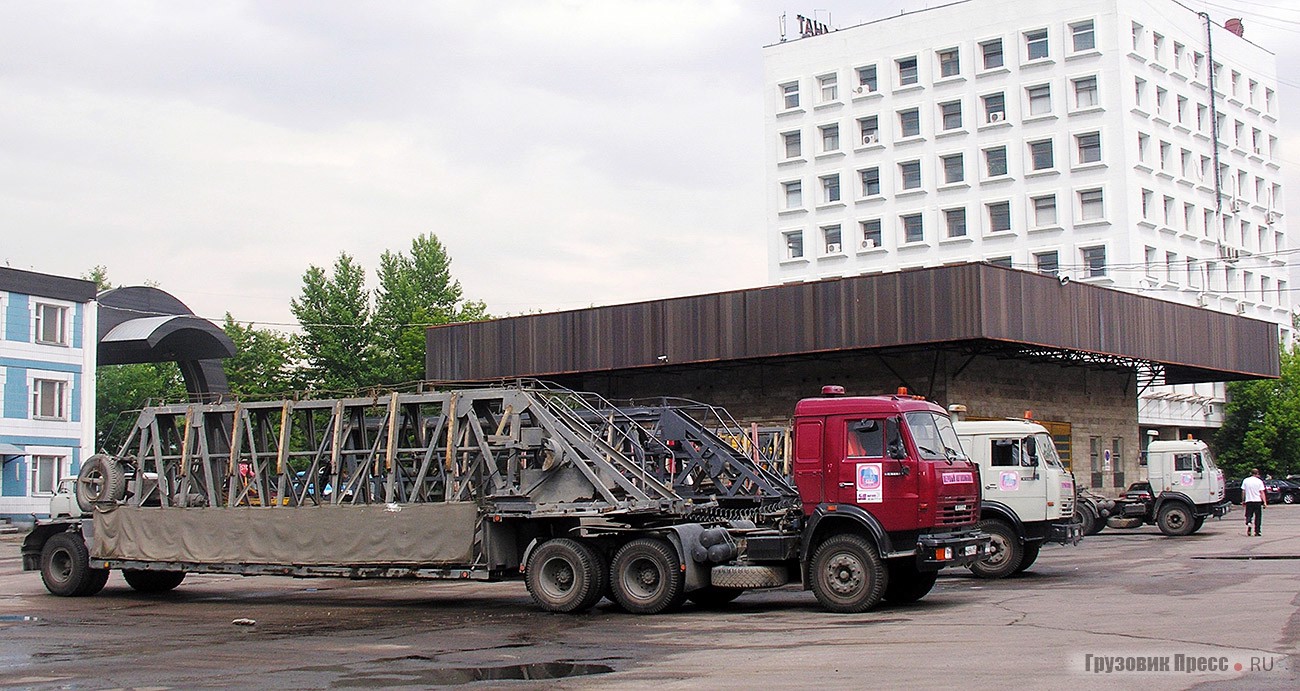
60 лет Первому автокомбинату им. Г.Л. Краузе
В нынешнем году крупнейшее автотранспортное предприятие Москвы, да и России, ОАО «Первый автокомбинат» им. Г.Л. Краузе отмечает своё 60-летие. Появлению автокомбината предшествовало постановление Совета Министров СССР в мае 1955 года, когда было создано Главное управление автомобильного транспорта Мосгорисполкома – Главмосавтотранс.
Гигант из прошлого
Первый автокомбинат с 1970-х остаётся настоящим гигантом автотранспортной сферы. Сейчас на балансе головного предприятия и шести его филиалов находится около тысячи грузовиков 60 различных моделей грузоподъёмностью от 0,8 до 35 т и почти 800 единиц прицепного состава 50 разновидностей. Это самый крупный парк в мире, сосредоточенный на одном предприятии. Предприятие в основном занимается перевозкой строительных грузов, отсюда и специализация подвижного состава: седельные тягачи КАМАЗ, МАЗ и в меньшей степени ЗИЛ для работы с полуприцепами ОдАЗ, МАЗ и др., а также бортовые машины и самосвалы на шасси тех же марок. Для перевозки мелкопартионных грузов служат Hyundai Porter H-100, Hyundai HD 78, УАЗ-3741 , ГАЗ-3302 «ГАЗель», ЗИЛ-5301 СС и ЗИЛ-5301ГО «Бычок». В последние годы списочный состав пополнился более чем сотней большегрузных Scania, Volvo и MAN. Вспомогательный транспорт для хозяйственных нужд представлен самосвалами, автокранами, масловозами, поливочно-моечными машинами, тракторами и пр.
Чтобы поддерживать столь обширный спектр автотехники в исправном состоянии создана мощнейшая производственная база. В арсенале находится порядка 4000 образцов гаражного оборудования и свыше 200 постов ТО и ремонта автомобилей, чего нет даже у очень крупных техцентров.
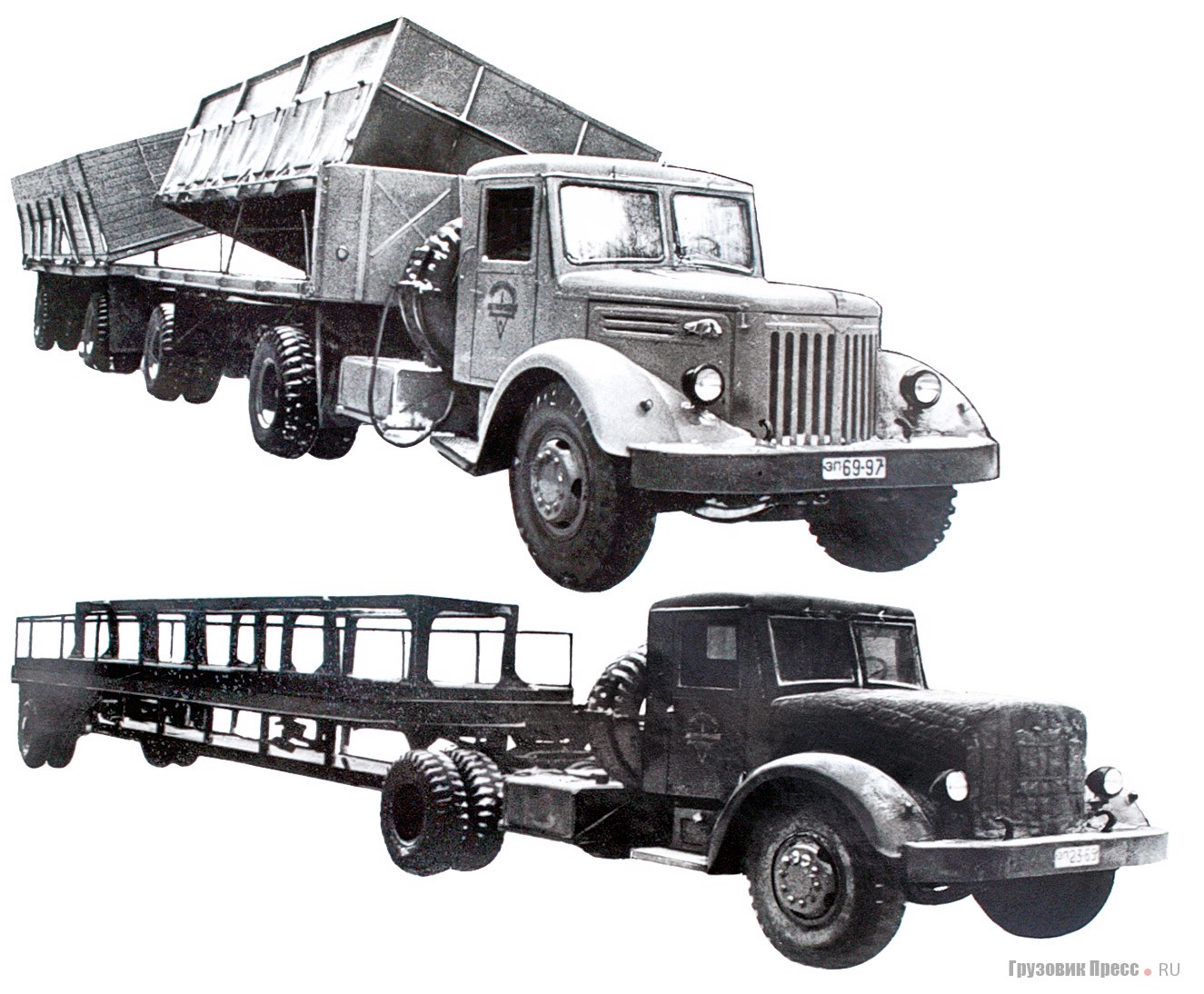
Ставка на собственные силы
Чтобы ежедневно выпускать свыше 700 машин на автокомбинате применяют планово-предупредительный ремонт. Для обслуживания и ремонта автомобилей в автохозяйстве организованы зоны, цеха и участки, в которых проводятся ежедневное обслуживание (ЕО), текущее обслуживание (ТО-1 и ТО-2), текущий ремонт (ТР), а при необходимости и капитальный (КР).
По сути, нет такого ремонта, который в АТП не смогли бы сделать, поэтому здесь не пользуются услугами сторонних организаций. Сервисными мероприятиями занимаются почти 300 ремонтников. Система ТО-1 и ТО-2 ещё с советских времен сохранена в прежнем объёме. Практика доказала эффективность проведения данных мероприятий, хотя многие российские автохозяйства приступают к ремонту техники лишь после факта выхода её из строя.
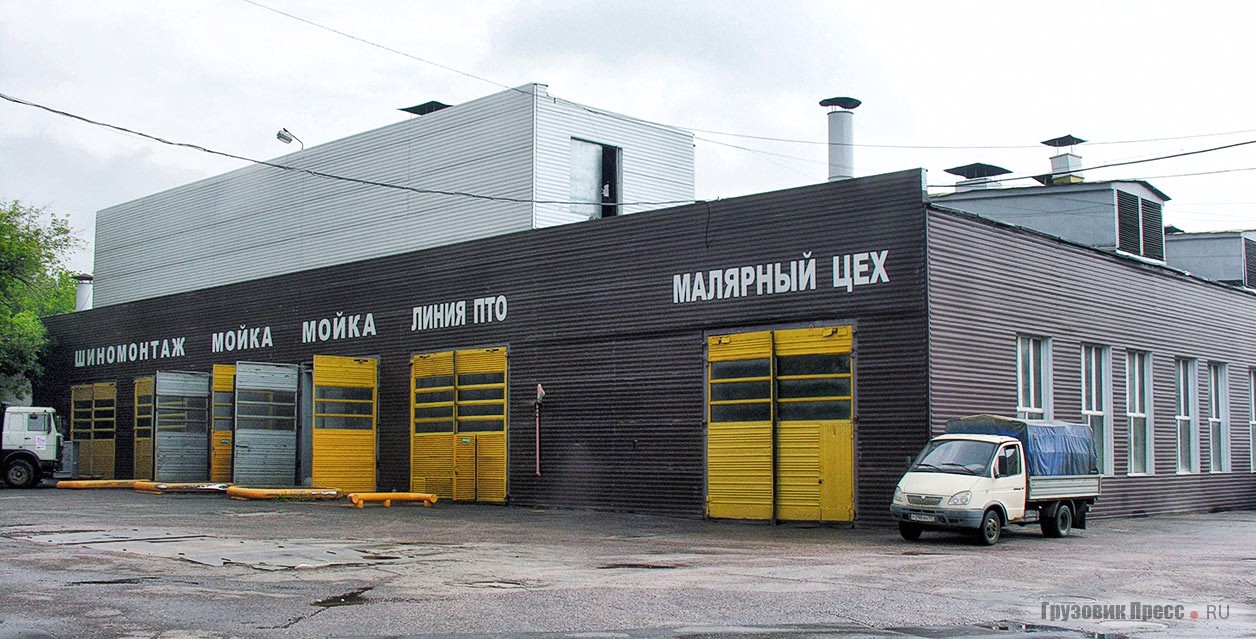
Для иномарок, находящихся в эксплуатации, существует иной порядок проведения регламентных работ, которые в АТП выполняются полностью. Для этого имеются необходимое количество смотровых канав и эстакад, разнообразное грузоподъёмное оборудование (кран-балки, электротали и пр.), многочисленные тупиковые и поточные канавы, подкатные и стоечные электромеханические подъёмники, маслораздаточные колонки, разнообразный инструмент и оснастка.
Участок по ремонту топливной аппаратуры следит за исправным состоянием топливных насосов высокого давления для дизелей различного типа (ЯМЗ-236, ЯМЗ-238, ЯМЗ-7511, КАМАЗ, ММЗ-245, а также другие нерядные ТНВД) и выполняет ремонт форсунок, карбюраторов и бензонасосов.
В цехе ремонта электрооборудования грузовиков и прицепной техники обслуживают и ремонтируют генераторы, стартёры, приборы светотехники, выполняют замену электропроводки и т.д.
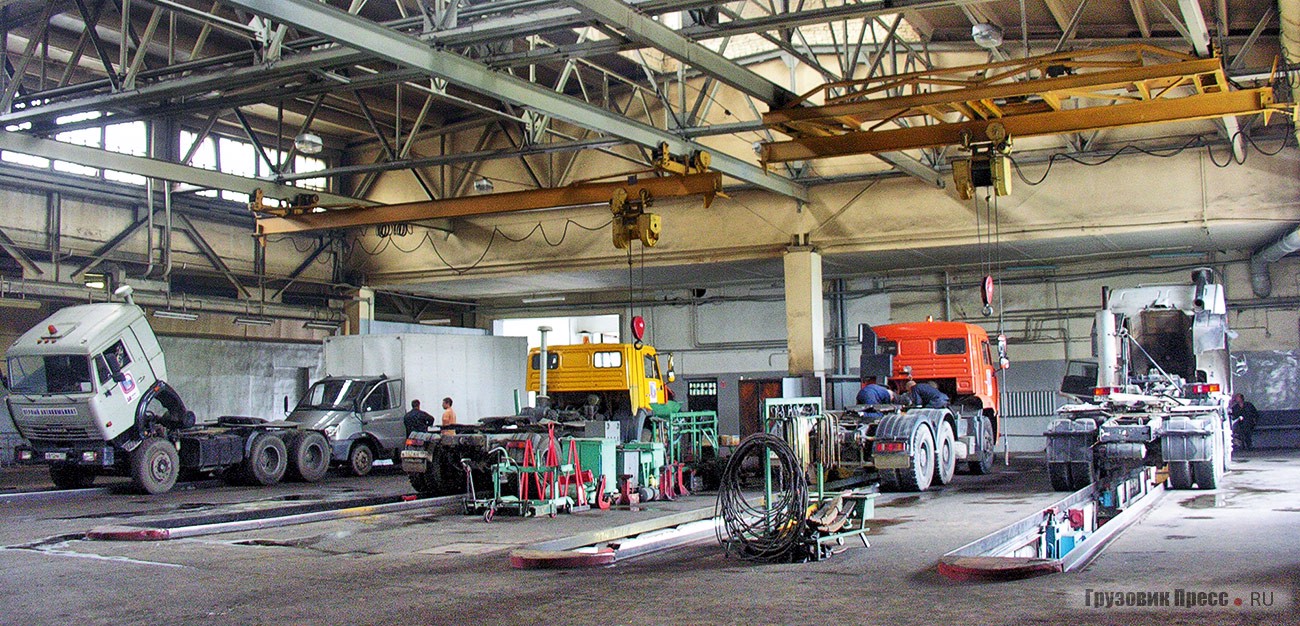
На участке по ремонту агрегатов и запасных частей благодаря ТР и КР реанимируют неисправные сцепления, коробки передач различных типов, редукторы ведущих мостов, агрегаты тормозной аппаратуры, гидроусилители, насосы рулевого управления, передние оси, пневмосистемы грузовиков, силовые гидроцилиндры для опрокидывания самосвальных кузовов, ССУ и т.д. Здесь же производится капремонт ДВС.
Используя производственный потенциал, в автохозяйстве не только восстанавливают изношенные узлы методом наплавки и дальнейшей механической обработки, но и при необходимости изготовляют оригинальные детали по чертежам, включая компоненты для импортных грузовиков.
На заготовительном участке хранятся и раскраиваются с помощью соответствующего технологического оборудования различные профили, стальной прокат, заготовки и пр.
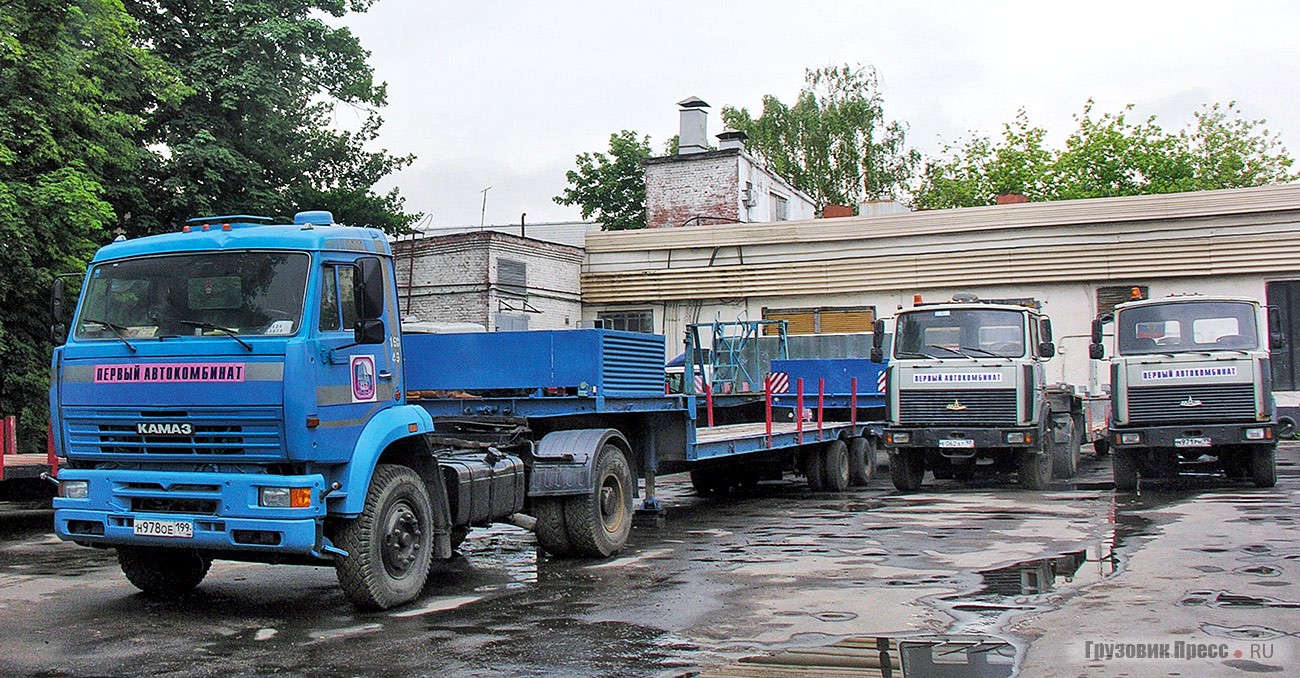
На механическом участке с помощью токарных, фрезерных, сверлильных, расточных, шлифовальных станков и другого оборудования изготовляют широкую гамму деталей и узлов для ремонта подвижного состава.
На кузнечном участке изготовляется целый ряд оригинальных деталей, включая рессоры как для грузовиков, так и для внутрихозяйственных работ.
Шиномонтажный цех оснащён необходимыми механизмами, воздушными компрессорами для накачки шин, электрическими гайковёртами.
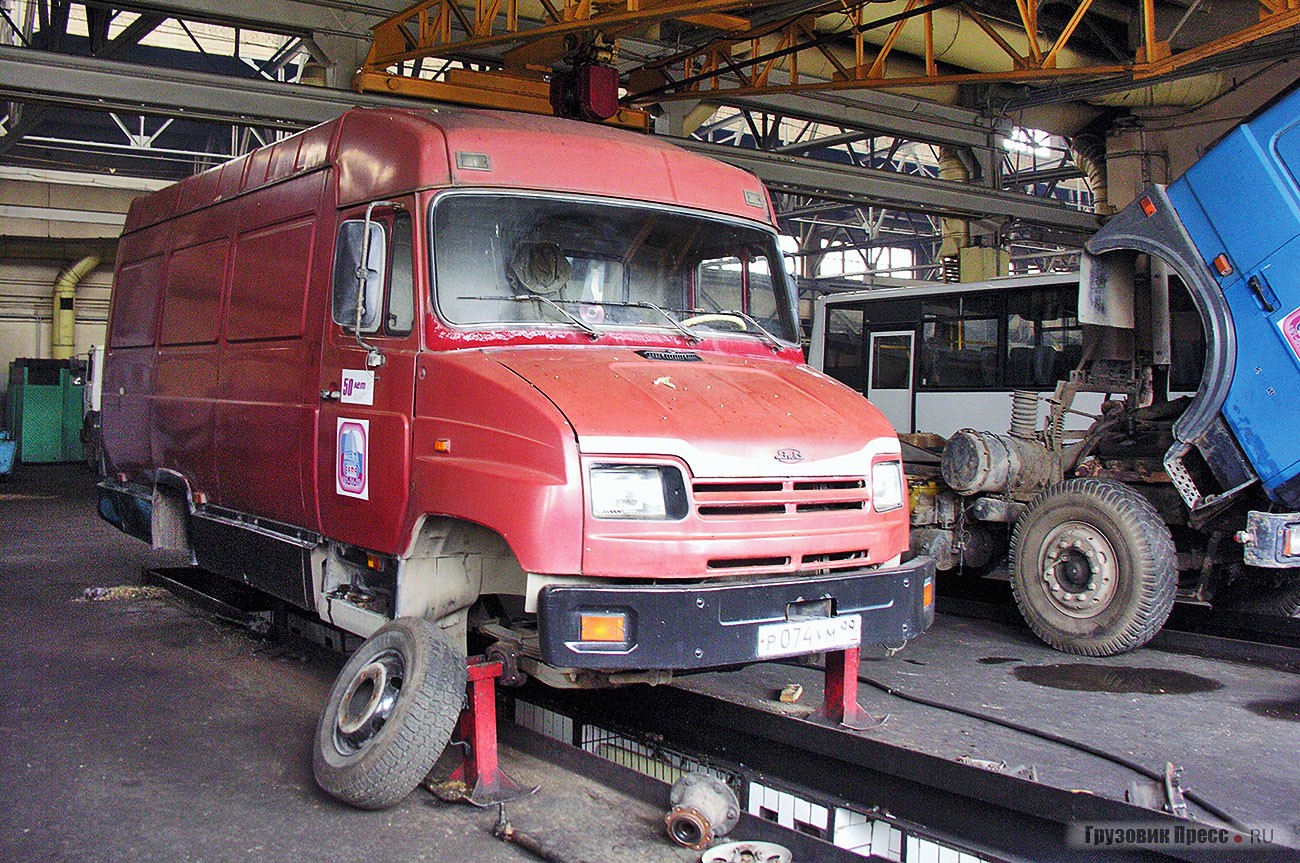
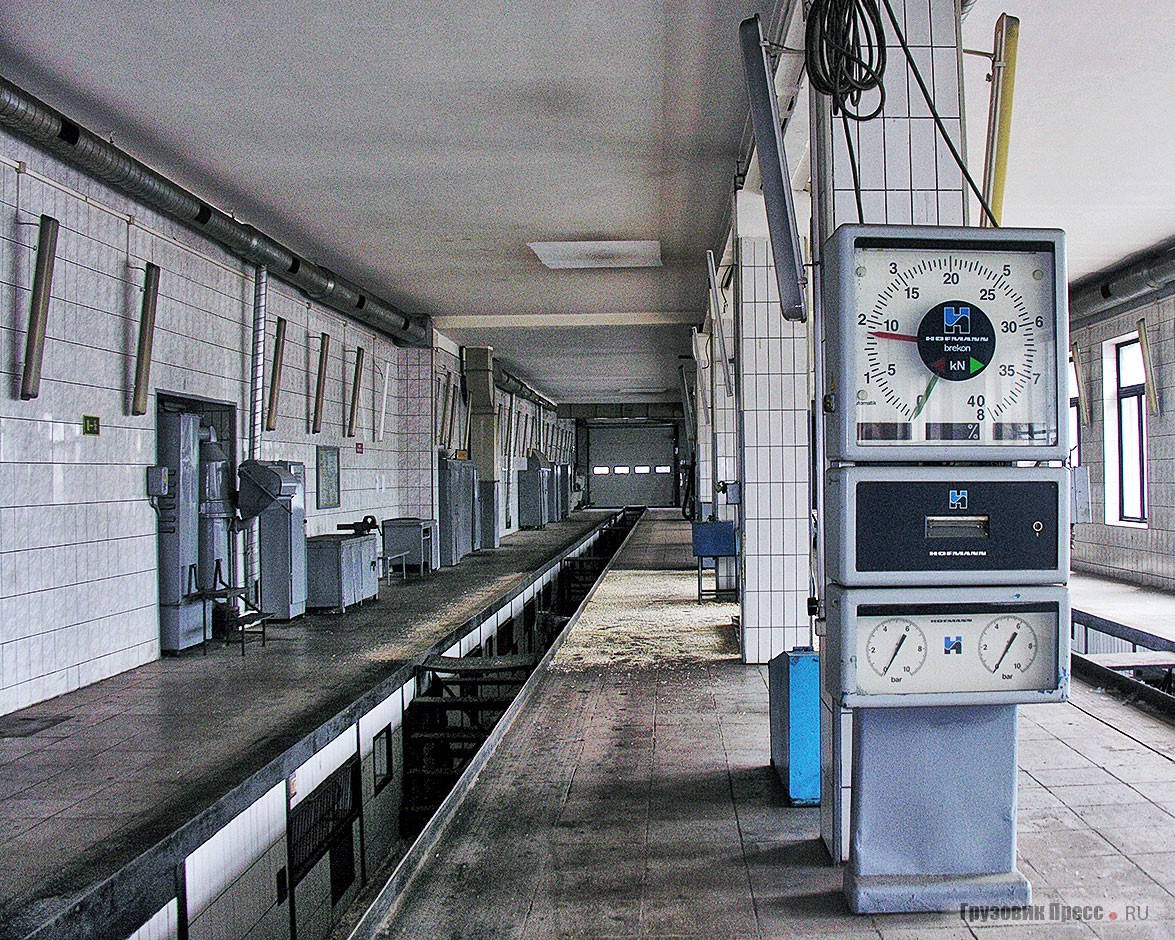
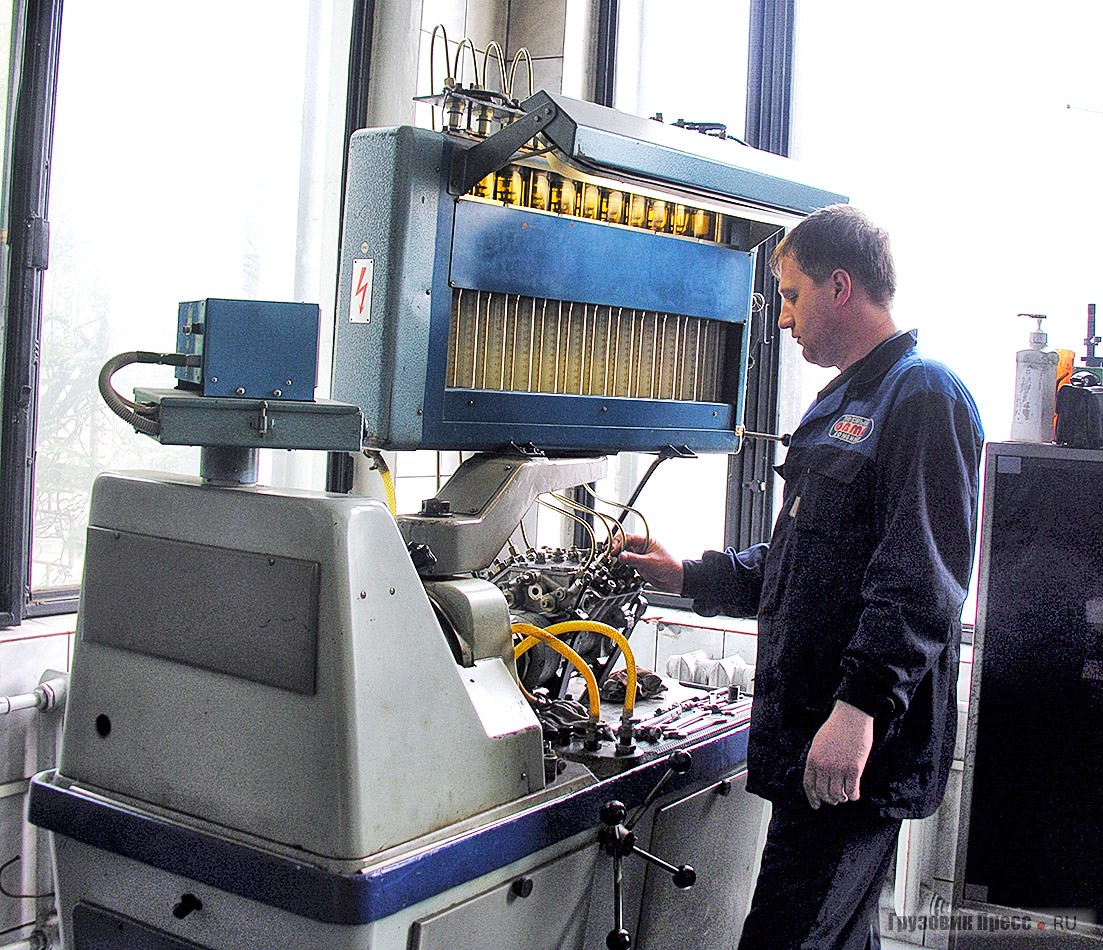
На автокомбинате максимально используются возможности диагностической линии, которая позволяет выполнять в том числе и государственный техосмотр автомобилей предприятия. Именно такое право комбинату делегировало ГИБДД. В состав оборудования входят диагностический тестер для определения неисправности двигателя, электронный люфтомер, газоанализаторы, прибор для проверки фар, тормозной стенд, диагностический прибор для проверки работоспособности АБС тормозов. Диагностическая линия предоставляет возможность с высокой точностью проверять мощность на ведущих колёсах автомобилей, расход топлива, содержание вредных выбросов в выхлопных газах, состояние систем и узлов двигателя, трансмиссии и ходовой части.
Подвижной состав, выходящий на линии, обязательно проходит через пост отдела контрольно-технического пункта. О показателях работы эксплуатационной и производственной служб убедительнее всего говорит коэффициент технической готовности (КТУ) подвижного состава равный 0,9, т. е. на предприятии при проведении ТО и ремонта находится не более 10% подвижного состава, если речь идёт об отечественных грузовиках. У автомобилей зарубежных марок ввиду их более высокой надёжности КТУ ещё выше, а ремонтозатраты напротив снижены.
Разработка технологических карт на ТО и ремонт автотехники ведётся в соответствии с указанием «Руководства по эксплуатации автомобилей и сервисного обслуживания», а также рекомендаций НАМИ и НИИАТ.
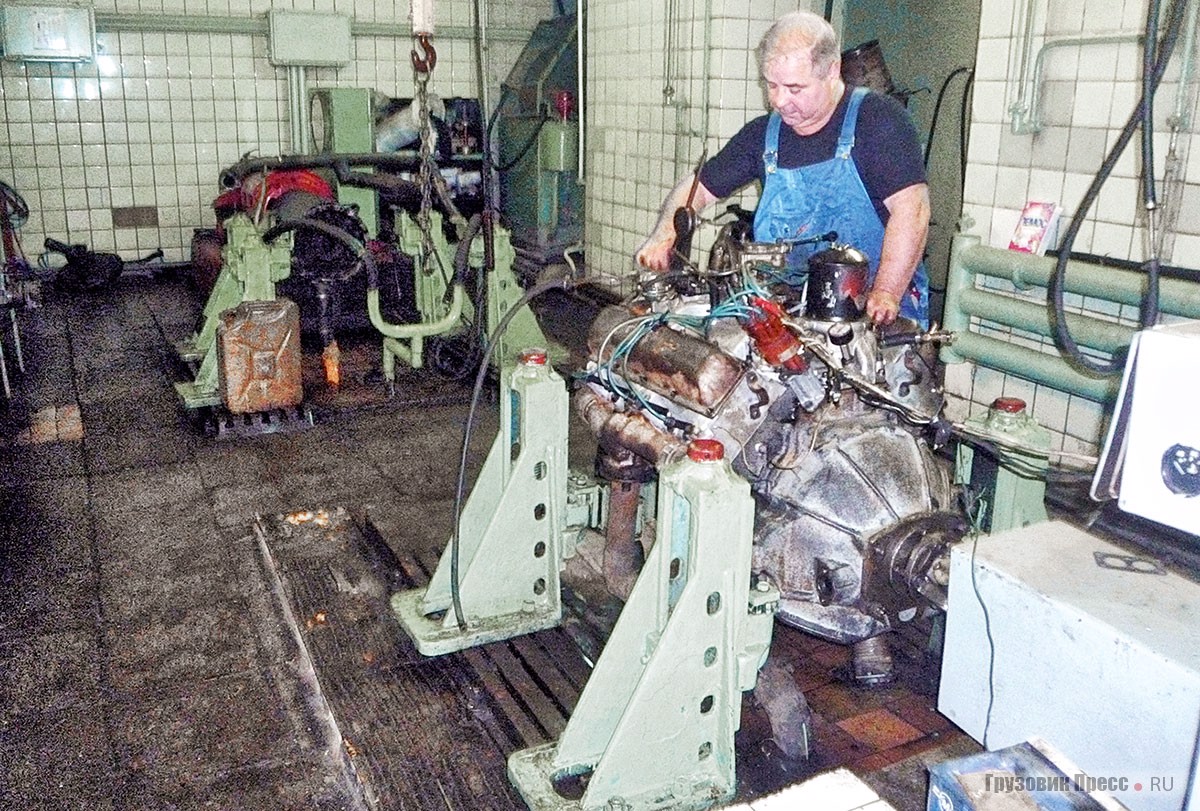
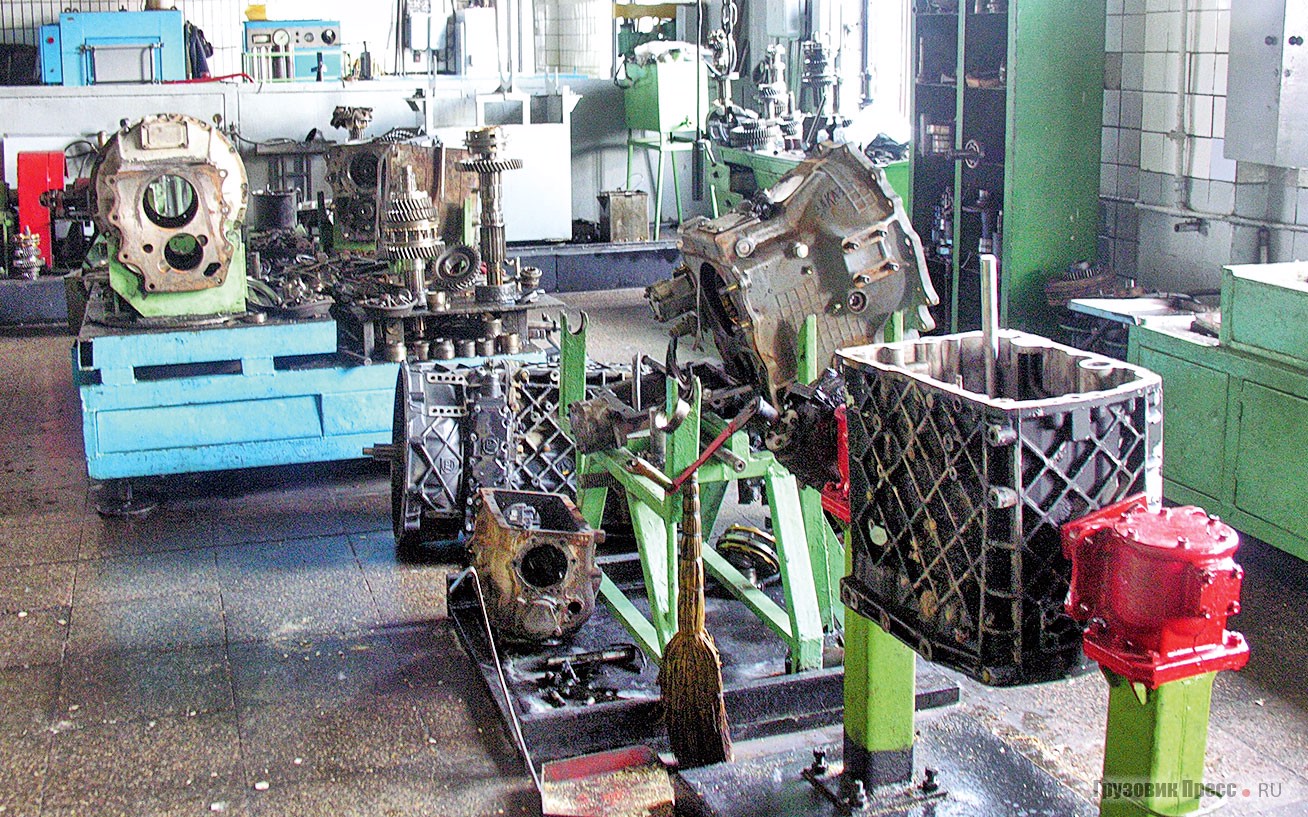
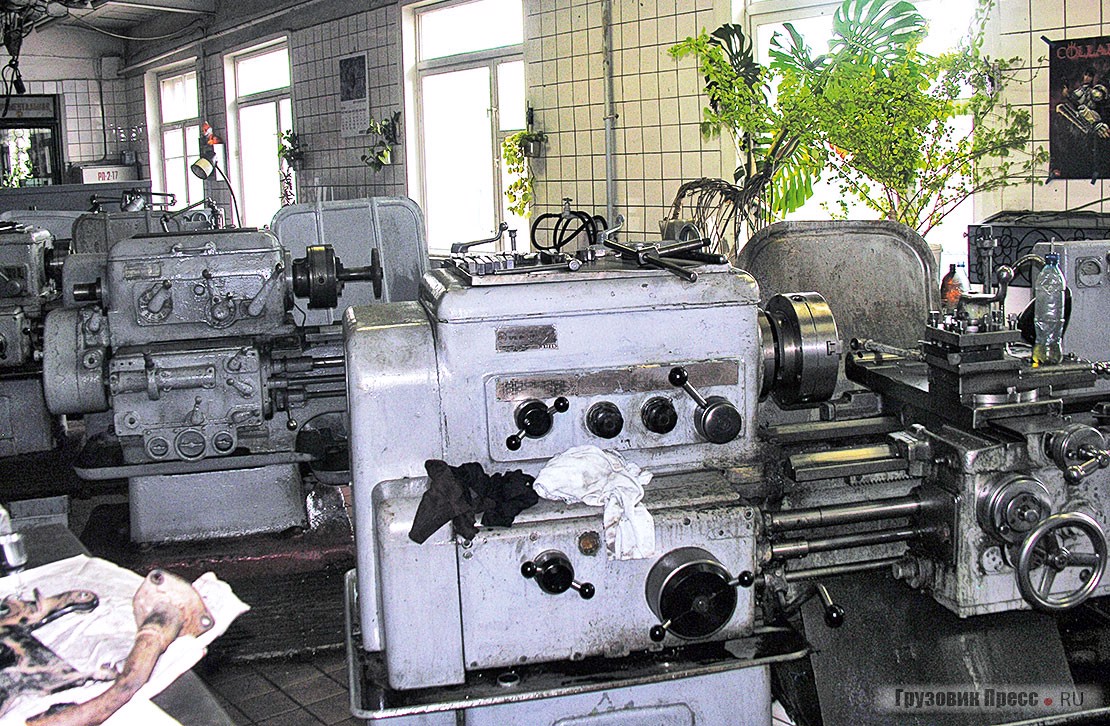
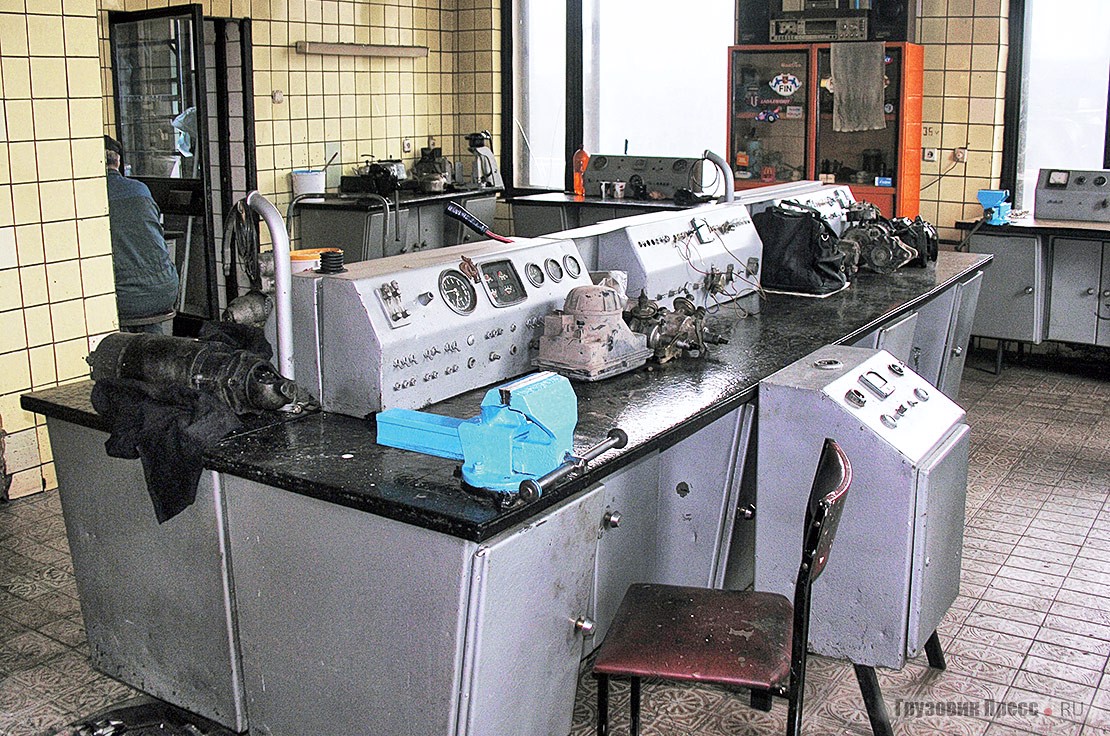
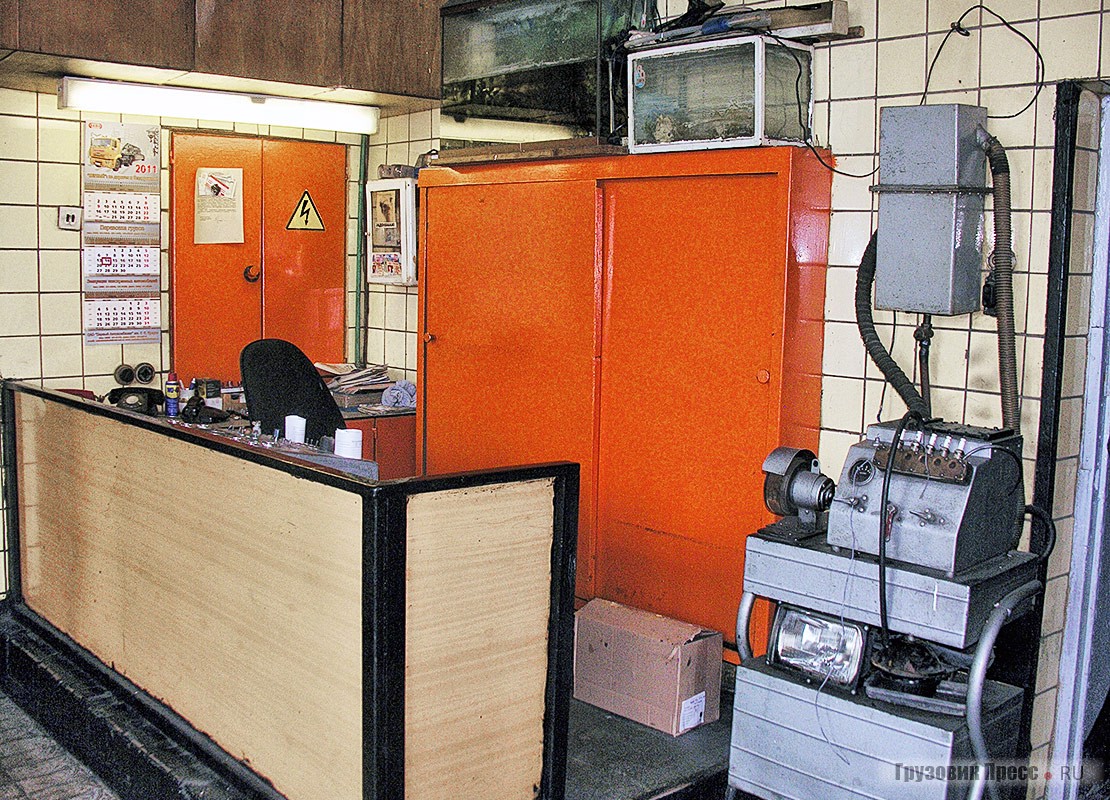
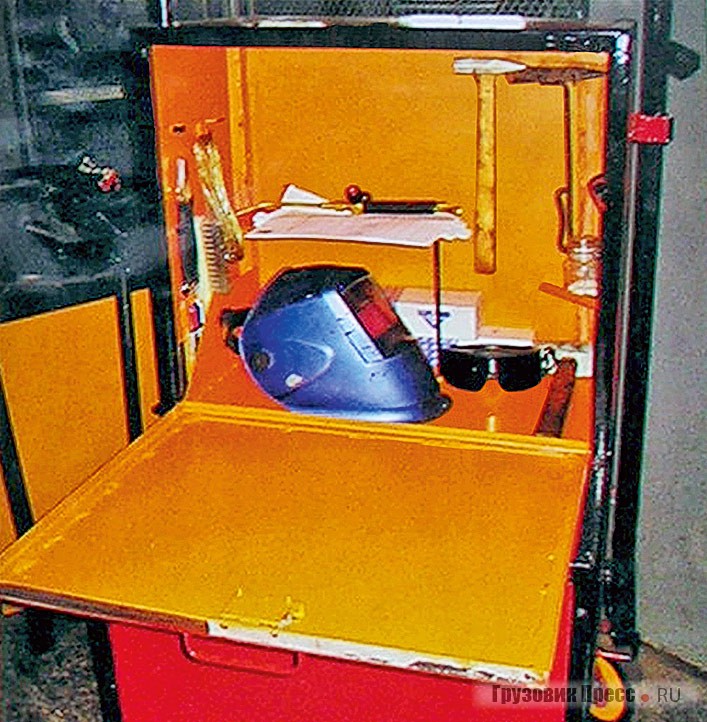
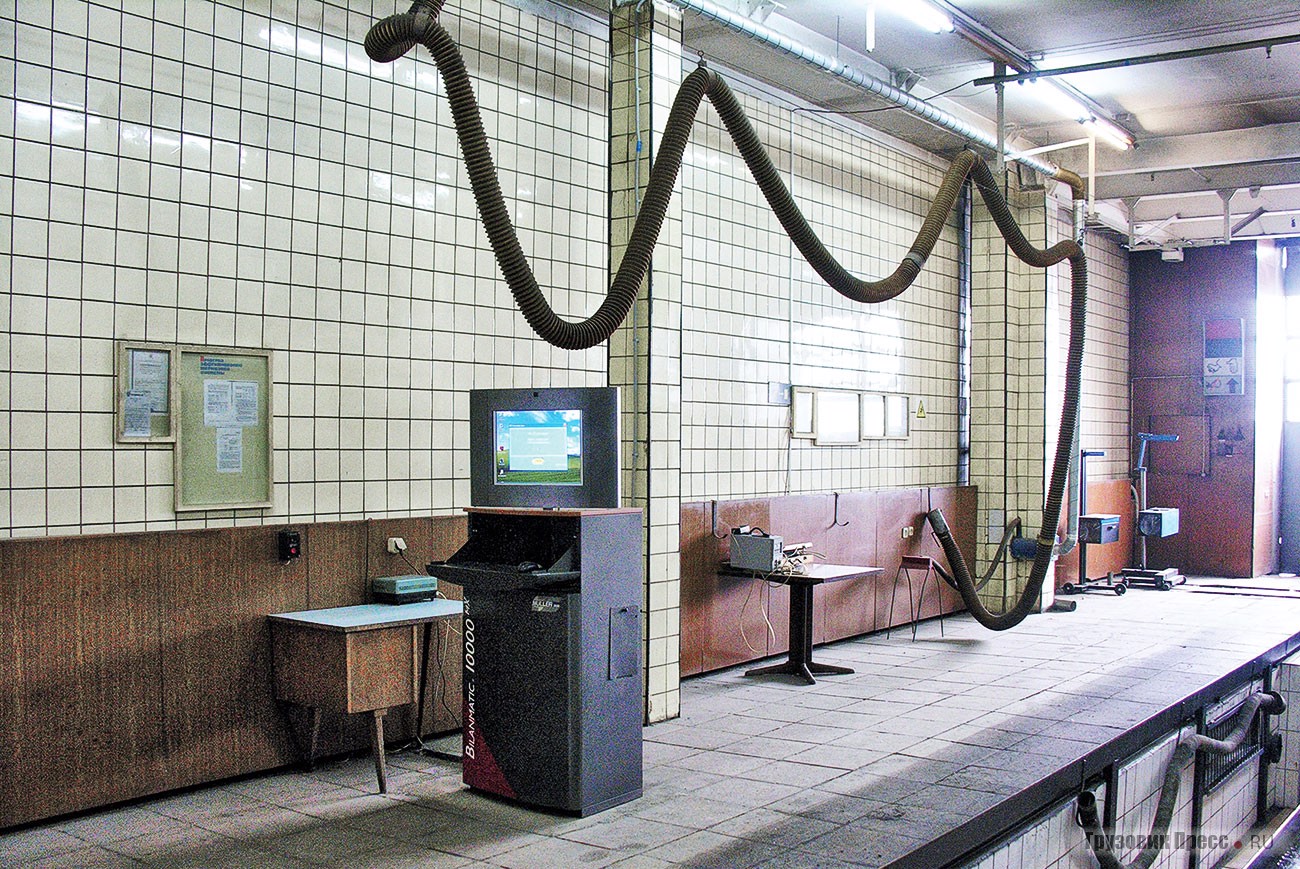
Движущие силы прогресса
Одной из ключевых особенностей автокомбината является высокий уровень технического творчества для решения конкретных задач при совершенствовании производственных процессов и повышении культуры производства. Именно здесь в конце 1970-х довели пробег автомобилей без капремонта до 350 тыс. км.

На предприятии с 1960-х сформировался свой регламент проведения творческой работы. Главные принципы: исключительно индивидуальный подход к каждому автору, его предложению, особенно внимательно относятся к молодым новаторам и быстрому вознаграждению. БРИЗ оценивает патентоспособность вероятных изобретений после каждого смотра, ходатайство о выдаче патентов и присвоении почётных званий.
Прологом к смотру служит производственное совещание. Совет из нескольких десятков человек, среди которых начальники цехов, мастера, бригадиры, рационализаторы, члены центральной и рабочей комиссий, обсуждают, что удалось улучшить по результатам последнего смотра.
За неделю до смотра рабочая комиссия, состоящая из ИТР во главе с генеральным директором Борисом Штерном, посещает подразделения для комплексной оценки по таким направлениям, как повышение производительности труда; механизация и автоматизация производственных процессов; восстановление и тиражирование ранее изготовленного высокоэффективного оборудования и приспособлений; улучшение качества продукции; эффективное использование материальных и трудовых ресурсов; повышение качества техобслуживания и ремонта автотехники, агрегатов, узлов и деталей; совершенствование технологических процессов и внедрение в производство достижений науки и техники и др.
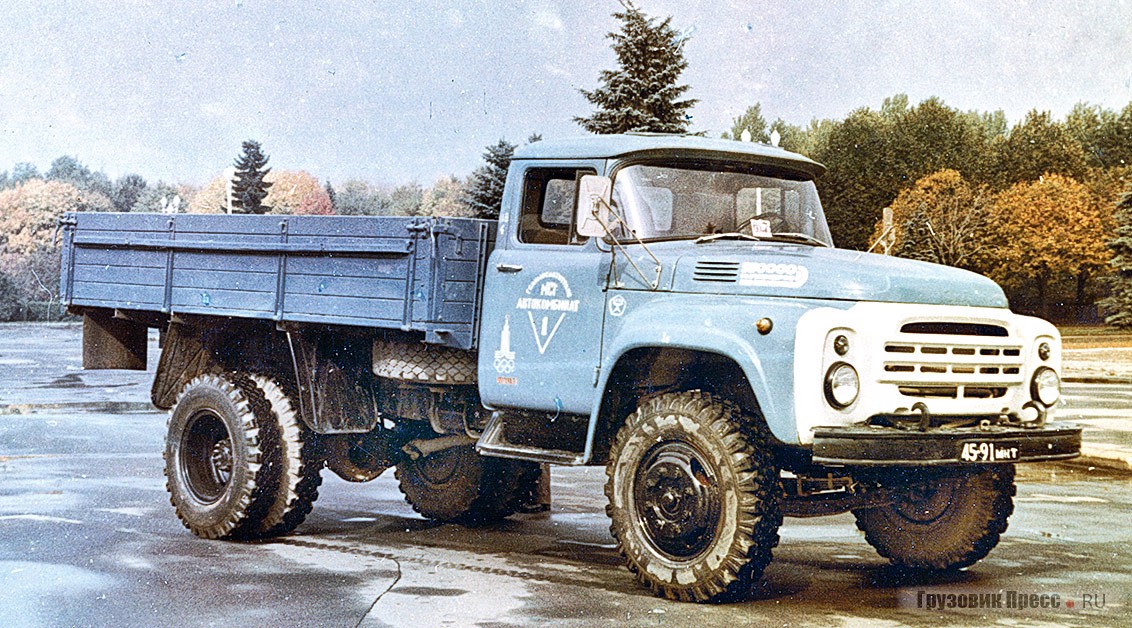
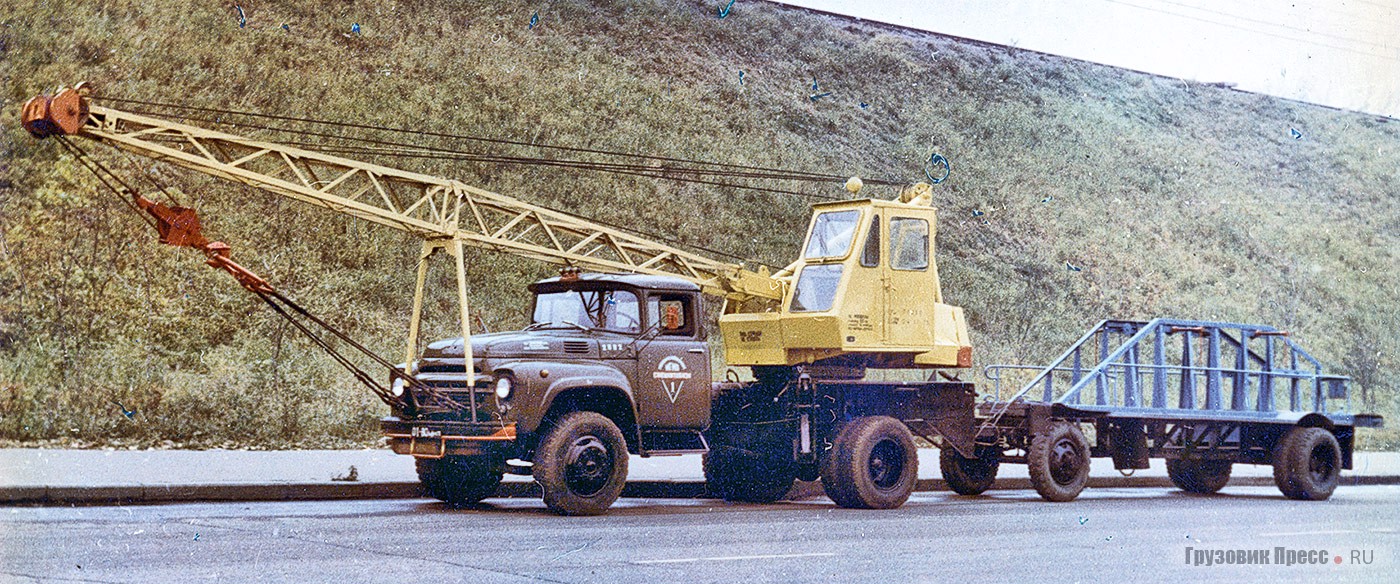
Назначаются соответствующие денежные премии. Определяют победителей среди цехов, лауреатов 1-й, 2-й и 3-й степеней.
Смотры новаторов – по-настоящему уникальное явление. Ничего подобного в аналогичных предприятиях не существует. Ежегодно на предприятии внедряются свыше 500 предложений рационализаторов.
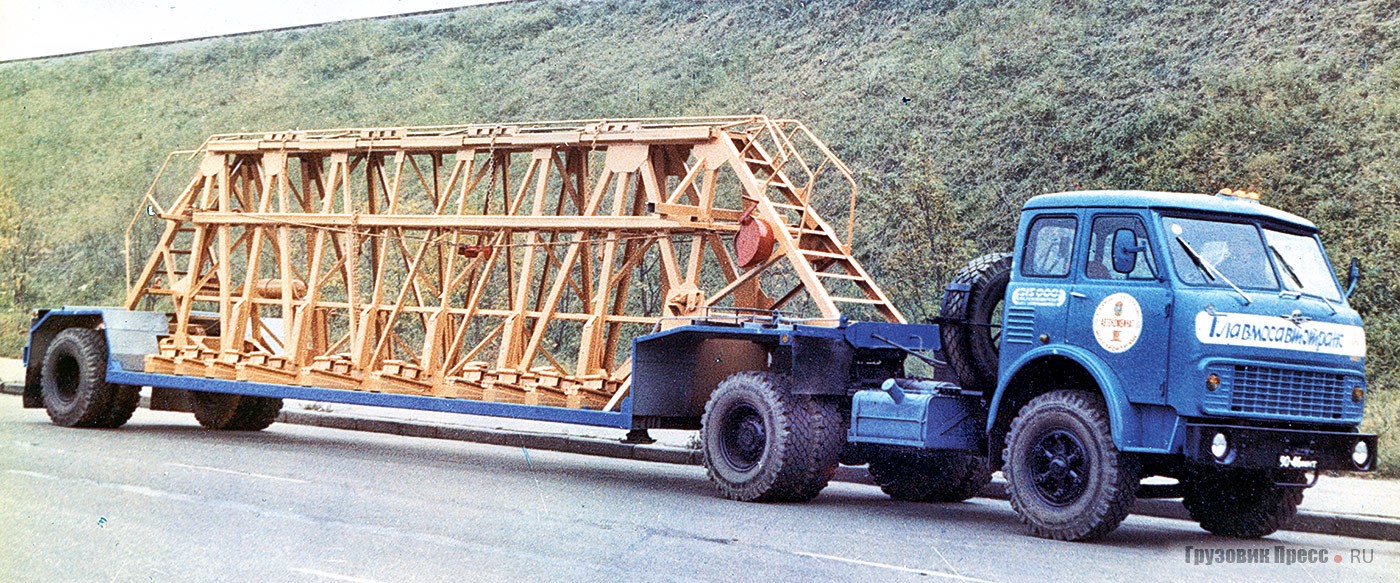
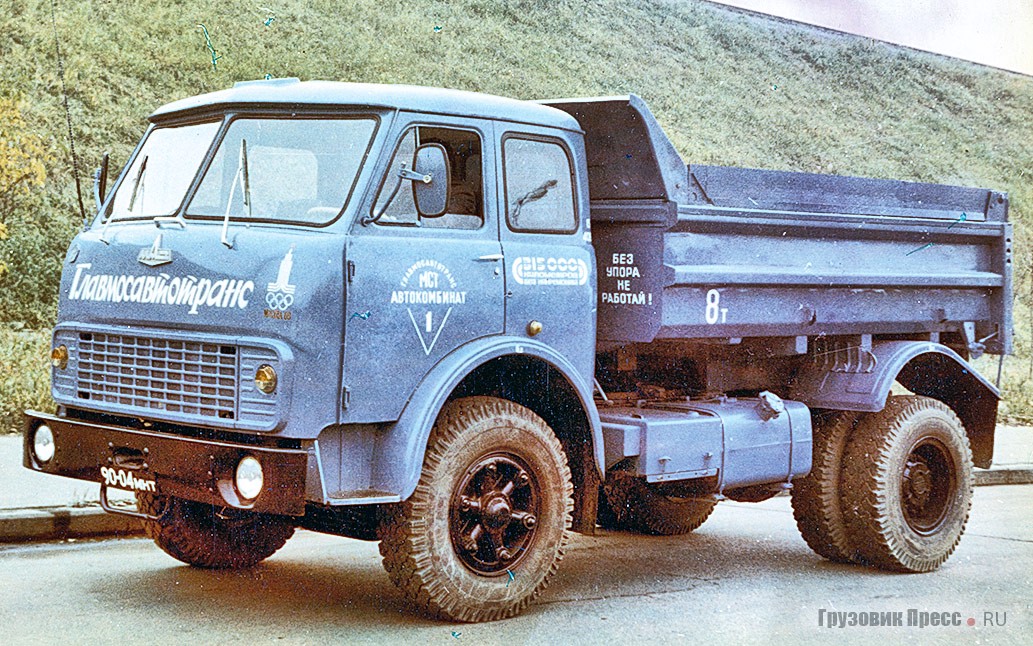
Взять хотя бы восстановление водяной рубашки двигателя вследствие кавитационного износа каналов в местах сопряжения деталей (вместо замены блока двигателя с соответствующим внесением изменений в учётные данные автомобиля) даже без снятия двигателя прямо на автомобиле. В числе свежих можно отметить: планшайбу для расточки уширенных колодок МАЗ-543203; передвижное место слесаря для замены ветровых стёкол; кондуктор для резки газосварочной горелкой швеллеров под разным углом; стенд для проверки рычагов поворотных кулаков; передвижное место сварщика; передвижной канавный гидромеханический подъёмник для демонтажа коробок передач.

Местные умельцы приспособили снятые с эксплуатации автомобили для перевозки различных грузов между подразделениями автокомбината. Базовыми моделями стали отслужившие своё машины. На ульяновской «буханке» вместо срезанной части кузова установили открытую грузовую платформу для транспортировки узлов и агрегатов (двигатели, КП, мосты) из ремонтной зоны в сборочную.
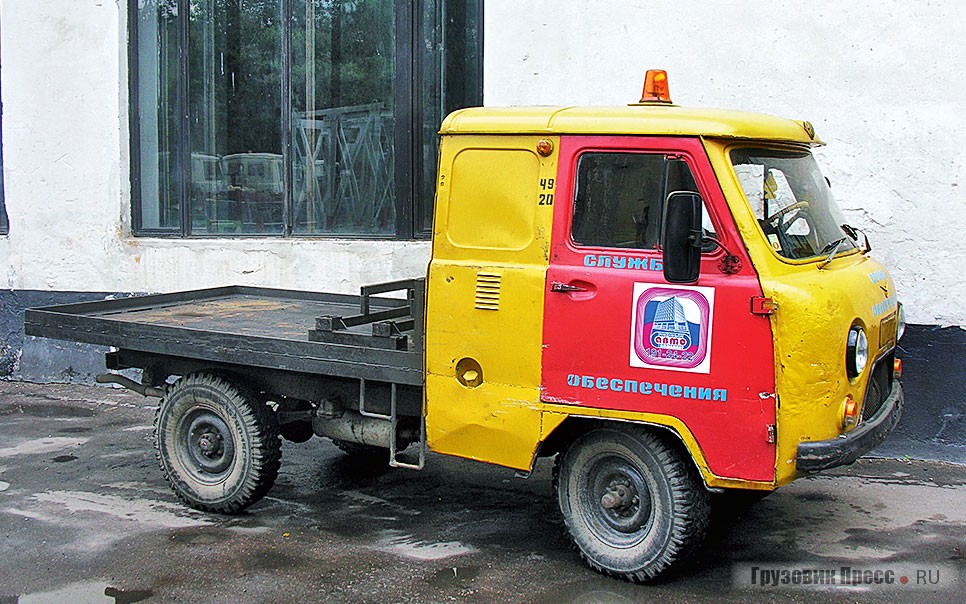
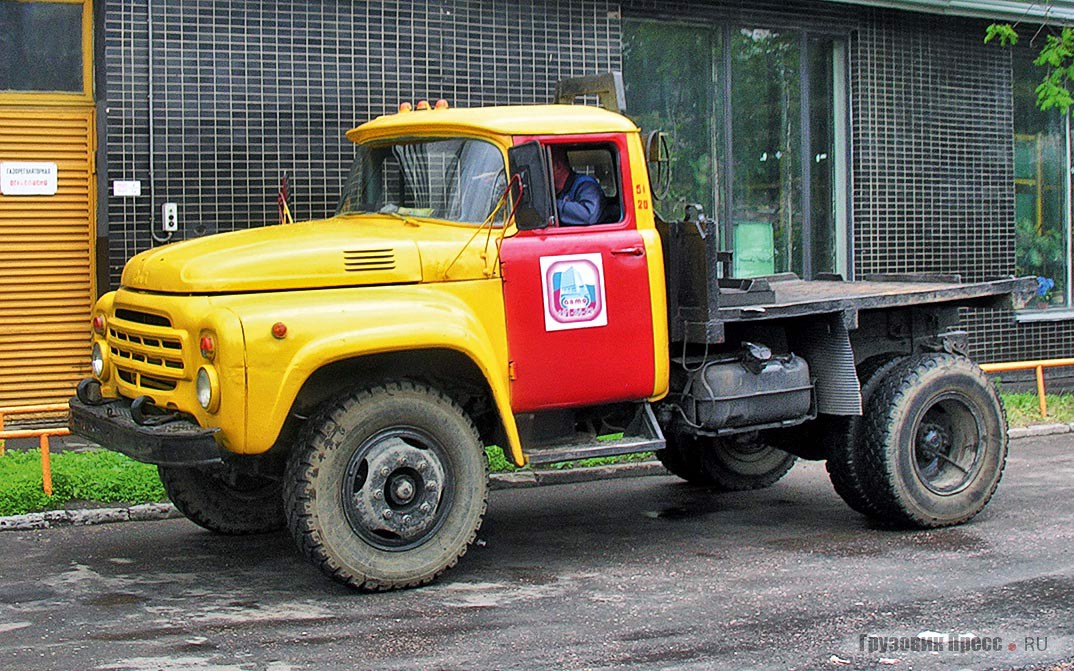
Аналогичным метаморфозам подверглись и дворовые грузовики ЗИЛ. На укороченной раме смонтирована стальная платформа с одним бортом, прикрывающим кабину, и механизмом для крепления груза. В технологическом процессе задействованы и автомобили технической помощи и ремонтные летучки.
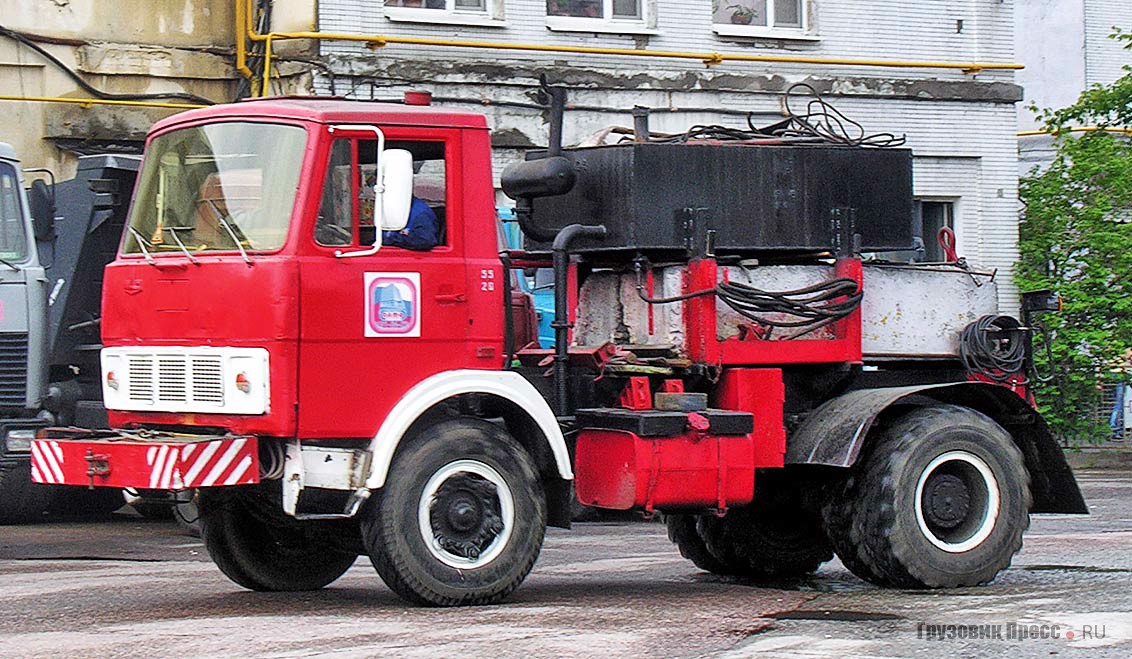
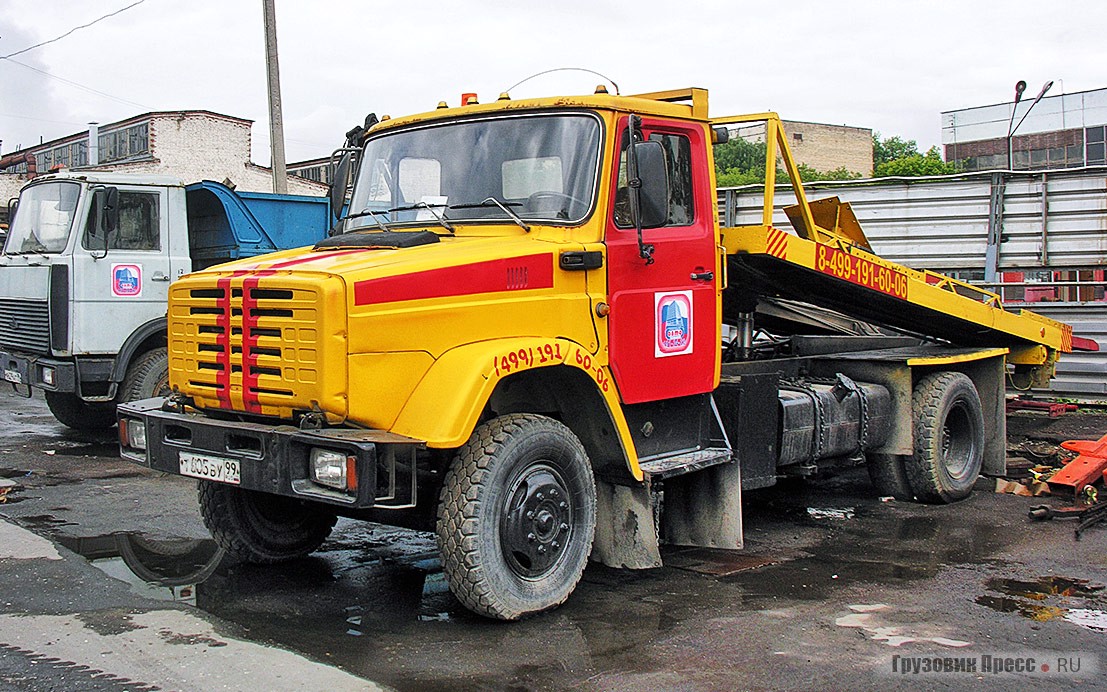
А ещё «кулибины» из Первого автокомбината на базе серийных машин создают тягачи, которые оборудованы разнообразными приспособления для вывешивания, буксировки, погрузки, крепления на платформах и пр. Для буксировки подвижного состава по территории предприятия сконструированы балластные тягачи. Так, для перевозки керамзита из двух бортовых полуприцепов создали самосвальный кузов вместимостью 40 м3, который может использоваться для транспортировки сборного железобетона.
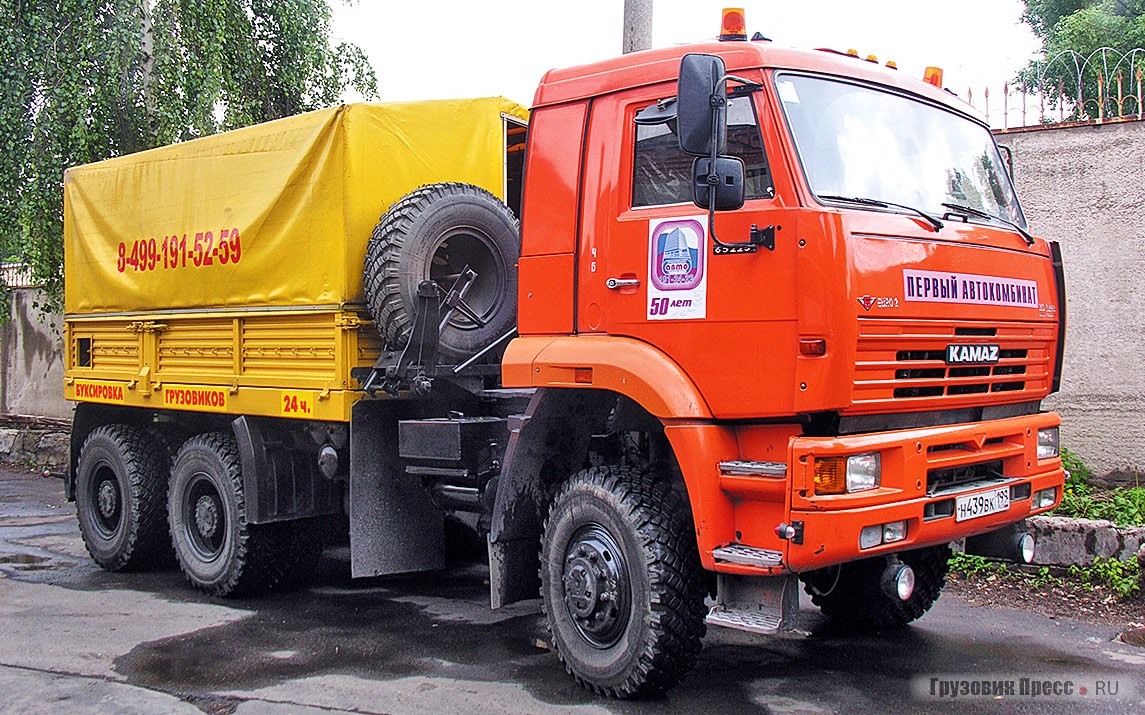