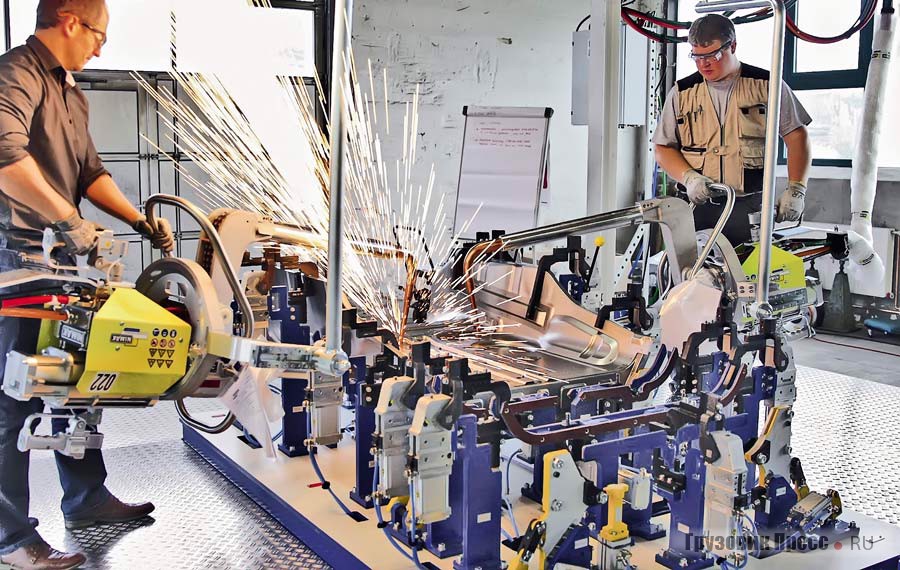
Далеко идущие планы
Проект «Кабина» ОАО «КАМАЗ» и Daimler AG
Пятнадцатое марта 2013 года стало знаменательным для ОАО «КАМАЗ». Именно в этот день начался первый этап проекта «Кабина». Да-да, разговор идёт о совместном детище ОАО «КАМАЗ» и его стратегического партнёра – компании Daimler AG. За прошедшие два года на автомобильном заводе построен новый конвейер кабин, на прессово-рамном заводе (ПРЗ) произведена модернизация окрасочной линии Durr, а с января 2014 года на «КАМАЗе» стали сваривать каркасы кабин для автомобиля «5490». Но эта новость уже старая. Дело в том, что в цехе сборки-сварки кабин прессово-рамного завода вновь происходят преобразования.
«КАМАЗ» ставит перед собой цель полного обновления модельного ряда. Один из главных пунктов достижения такой задачи – новая кабина. Этот проект безвозвратно преобразит облик популярного оте-чественного грузовика, да и что там говорить – полностью изменит весь «КАМАЗ». Этот проект – удачная демонстрация того, насколько эффективным может быть сотрудничество двух сильных компаний.
Высокотехнологичный островок
Новый участок в цехе сборки кабин появился в августе 2013 года, во время корпоративного отпуска. Но первые кабины были собраны только в октябре этого же года. Главная артерия потока – это напольный «транспорт», который движется по рельсам, а главный её плюс – организация производства сборки кабин любой конфигурации: с высокой и низкой крышей, с двумя спальными местами и без спального места. Конвейер предельно экономичен – для приведения его в движение не требуется электроэнергия, кабины просто передвигают по сборочным станциям вручную. Для этого были разработаны и изготовлены специальные удобные тележки, на конвейере смонтированы направляющие. Конвейер технологичен – он позволяет наладить сборку любых моделей кабин. Конвейер эргономичен, поскольку для его построения потребовалась сравнительно небольшая площадь, и в то время руководство «КАМАЗа» это очень устраивало.
На ныне действующем участке сборки кабин, конечно, нет завораживающего масштаба производства и главного чуда – превращения листа металла в каркас кабины. Это лишь желанная цель. Тем не менее этот высокотехнологичный островок – результат реализации инвестиционного проекта. На ПРЗ производство нового продукта решили строить в соответствии с принципами ПСК «КАМАЗ» и так преуспели в этом, что кое в чём даже обогнали завод «Даймлер» в Аксарае.
Если на предприятии в Турции линия по сборке каркасов кабин вытянута в длину, то на прессово-рамном заводе старт и финиш находятся в двух шагах друг от друга. U-образная компоновка экономит место и время при перемещении деталей. При этом число станций осталось прежним – десять, а дополнительные указатели не дадут перепутать комплектующие для правой и левой стороны.
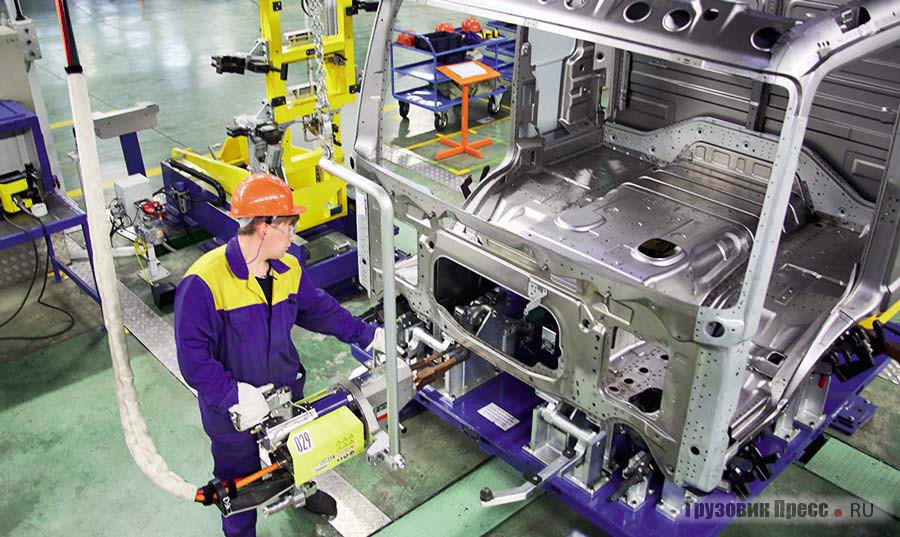
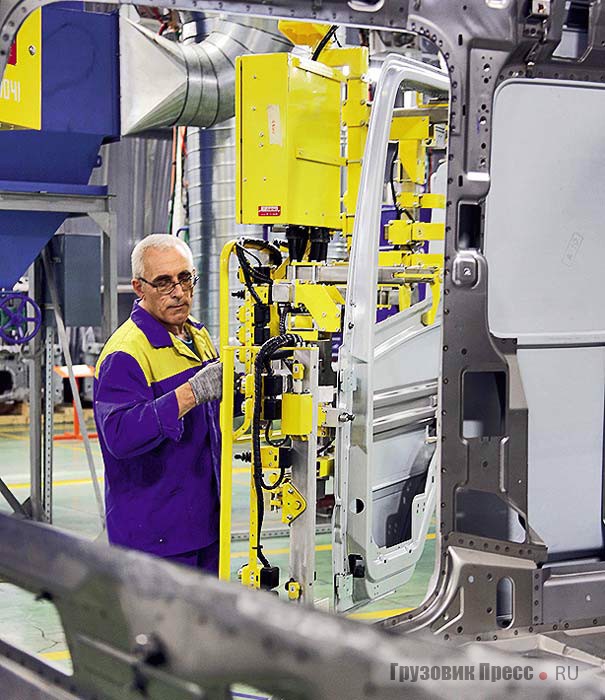
Технология, которая устарела за год
Методам технологии сборки и обращению с новым инструментом своих коллег обучали прессоворамщики, проходившие стажировку в Австрии на заводе Prototypen-Tech, который и стал поставщиком оборудования. И между прочим, в начале сборки кабин был обнаружен дефект комплектующих, из-за которого на время даже была приостановлена сборка машин КАМАЗ-5490. После расследования, проведённого специалистами компании Daimler, немецкие партнёры признали вину. Микротрещины на каркасах сначала исправляли специалисты, прибывшие из Аксарая, а затем к работе подключили прессоворамщиков.
Методы, которые сейчас используют при сборке кабин, по сути, копия технологии компании Daimler. Таким же образом кабины собираются в Турции и в Бразилии. При этом используются самые современные инструменты и сварочное оборудование, а также решения, оптимизирующие производительность этого оборудования.
Сейчас узлы приходят на сборку комплектом: одна кабина – один ящик с комплектующими. В комплект входят пол, крыша, задняя стенка в сборе с боковинами, передок, двери, крепёжные элементы. Иными словами, всего четыре крупных узла, из которых сваривают каркас кабины, а потом навешивают двери. Понятно, что в таком ящике с комплектующими бо’льшую часть пространства занимает воздух. И перевозка этого воздуха из-за границы морем до Санкт-Петербурга, а оттуда автотранспортом – обходится заводу «КАМАЗ» весьма недёшево.
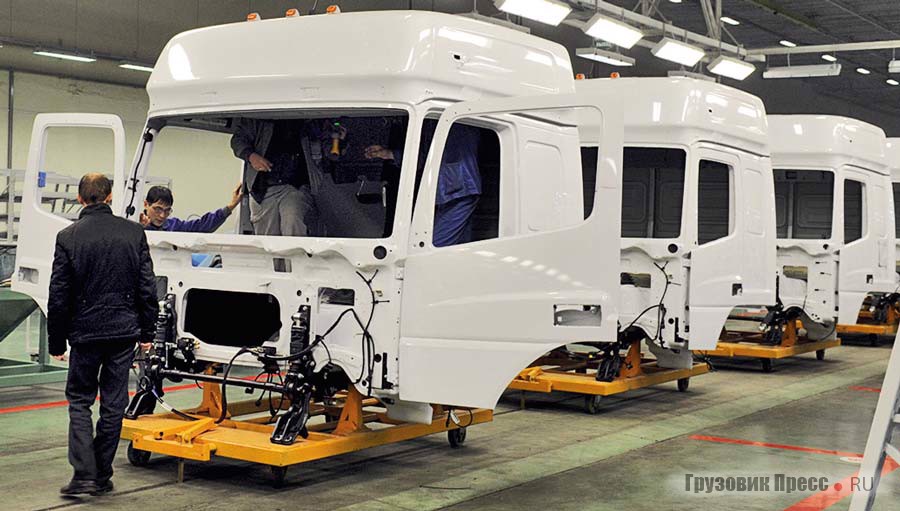
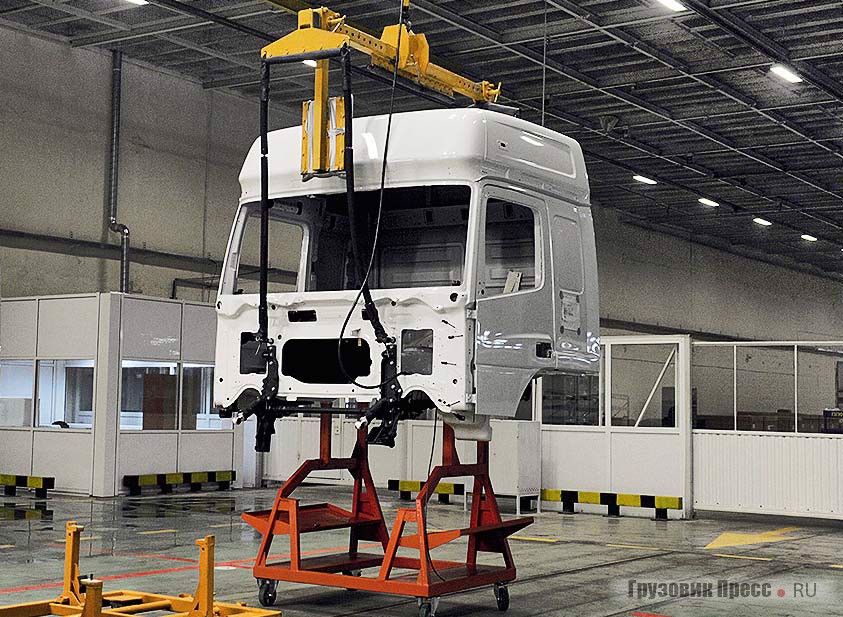
Есть ещё один нюанс: сегодня кабину с высокой крышей грунтуют отдельно. Это вынужденная мера, так как габариты установки катафорезного грунтования не позволяют пропустить высокую кабину в сборе. Для их стыковки в цехе окраски кабин установлена камера приварки высокой крыши. Защиту от коррозии в местах сварки обеспечивает специальный токопроводящий грунт.
Сегодня активно ведутся работы по переходу на следующий этап сборки кабин, который подразумевает более глубокую локализацию сварочных процессов.
Нечаянное импортозамещение
Совсем скоро вместо сборочных комплектов, по шесть крупных узлов в каждом, на конвейер будет поступать 174 позиции более мелких деталей, из которых они состоят. Новая линия сварки нужна как раз для соединения этих основных узлов, которые по уже освоенной технологии превращаются в каркас новой кабины.
Поставка отдельными деталями даёт возможность более плотной загрузки контейнеров, что намного сократит объём перевозок. Один и тот же морской контейнер сейчас вмещает всего четыре комплекта, а скоро будет перевозить деталей на 18–20 каркасов новой кабины. При поставке отдельными деталями примерно на треть снизится стоимость комплектующих, стоимость упаковки – на две трети, транспортные расходы и таможенные пошлины упадут до 25% от прежнего уровня. В итоге снижение себестоимости кабины составит около двух тысяч евро.
К моменту выхода этого журнала подготовительные работы войдут в завершающую фазу и начнётся плавный переход к работе с мелкими узлами. При этом произойдёт некоторое снижение объёмов комплектной поставки крупных узлов и наращивание собственного производства из отдельных деталей. То есть налицо программа импортозамещения в кризисный период. Однако все процессы по переоборудованию линии и сборке кабин по-новому завершатся только к концу 2015 года.
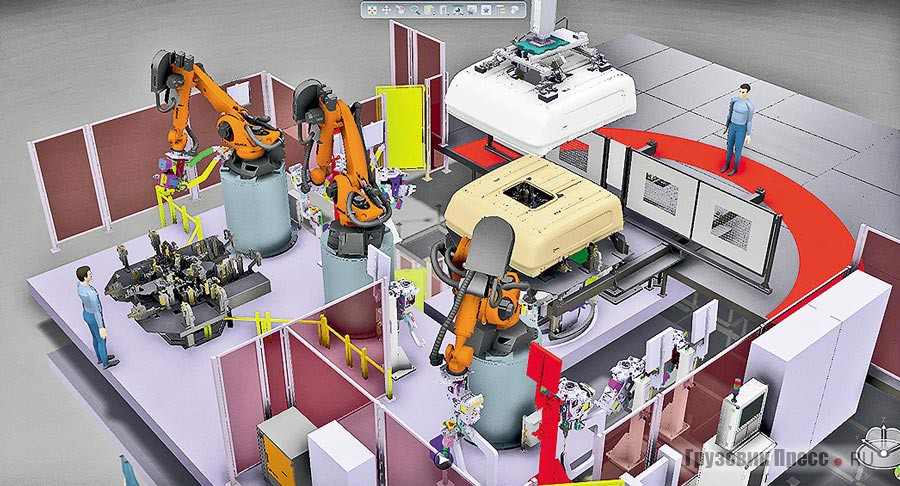
На уровне лучших образцов
Есть и другие мероприятия по переоснащению новой линии сборки кабин. Например, заключён контракт с зарубежной фирмой на модернизацию окрасочной линии. Покраска будет осуществляться роботами, как на лучших предприятиях мирового автопрома. В планах «КАМАЗа» – использование современных манипуляторов фирмы Camozzi. Они позволят значительно увеличить производительность труда и высвободить персонал для выполнения других видов работ. А чтобы всегда осуществлять жёсткий контроль по качеству новых кабин, на ПРЗ будет смонтирована измерительная лаборатория, аналогичная используемой компанией Daimler.
И ещё. Поскольку КАМАЗ-5490, соответствующий экостандарту Euro 5, содержит электронные системы управления, на рабочих местах сборщиков будет установлено современное оборудование для программирования и параметрирования электронных систем и проверки работы электрооборудования.
В общем всё на уровне!
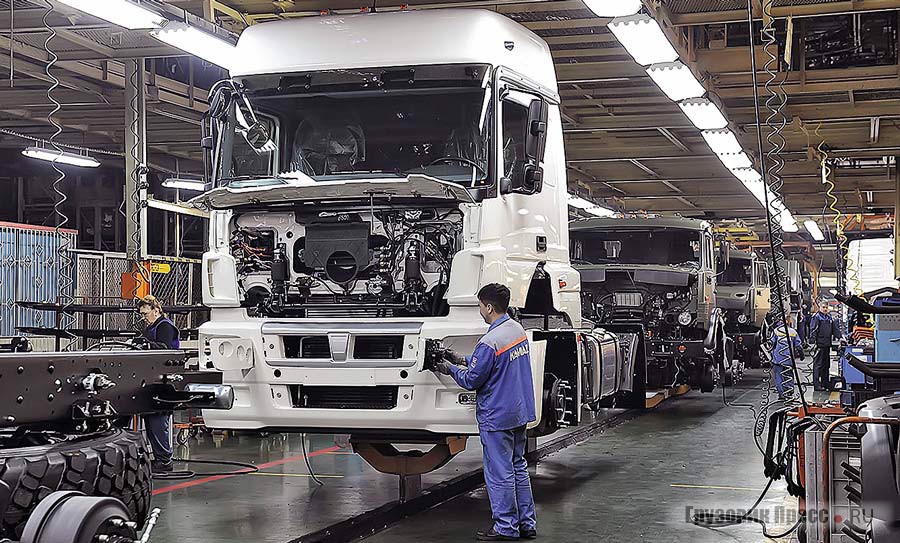