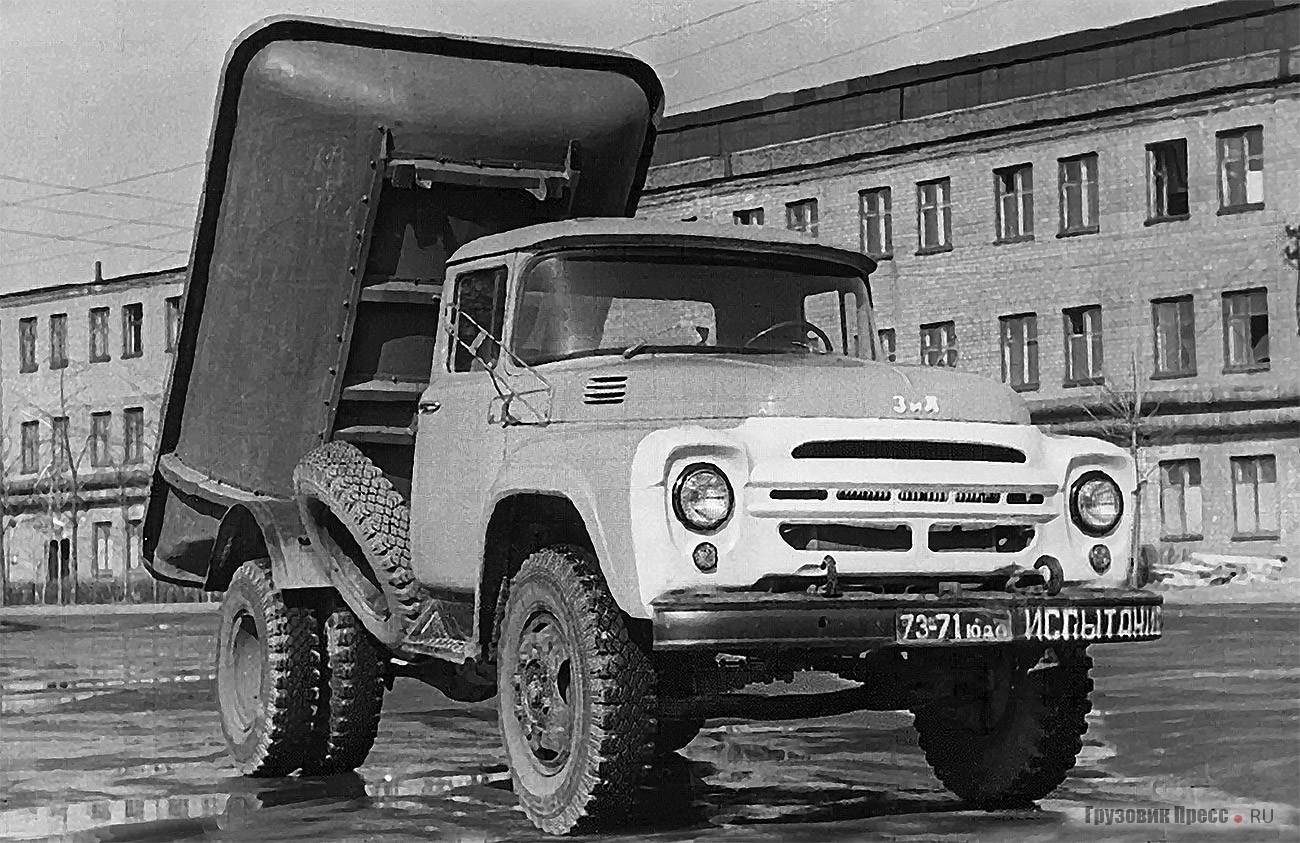
Пластмассовый самосвал
Cамосвал ЗИЛ-ММЗ-555Д с кузовом из стеклопластика
Появление этого автомобиля оказалось весьма своевременным. На рубеже 1950–1960-х гг. в отечественном автомобилестроении велись обширные опытно-конструкторские работы по внедрению новых синтетических материалов. Именно тогда были созданы знаменитый микроавтобус «Старт», началось производство стеклопластиковых кабин для многоосных шасси ЗИЛ и МАЗ, создавались опытные образцы малолитражных легковых автомобилей в НАМИ и МВТУ им. Н. Э. Баумана.
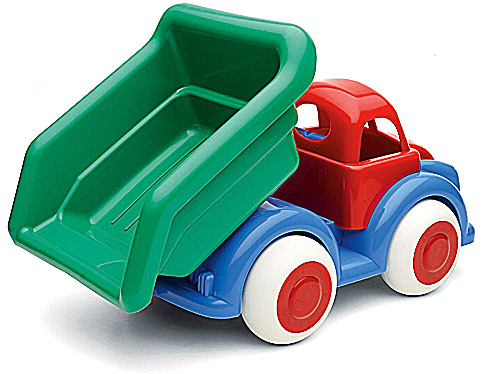
Не остался в стороне от этой тенденции и Мытищинский машиностроительный завод, освоивший к тому времени серийный выпуск 4,5-тонного автомобиля-самосвала ЗИЛ-ММЗ-555. В 1964–1965 гг. Отделом главного конструктора по автомобильному производству в опытном порядке был разработан самосвал с кузовом из стеклопластика, получивший индекс ЗИЛ-ММЗ-555Д. Ведущим конструктором по машине стал А.С. Мелик-Саркисьянц, впоследствии главный конструктор ММЗ по автомобильному производству.
Следует отметить, что в некоторых источниках, в том числе и заводских, этот автомобиль обозначается как ЗИЛ-ММЗ-555ПЛ («ПЛ», очевидно, означает «пластиковый»). Такое различие в обозначениях одного и того же автомобиля, по-видимому, можно объяснить тем, что на предприятиях отрасли не существовало системы индексации опытных образцов.
Причинами, по которым стеклопластик был выбран основным материалом в столь необычной для него области кузовостроения, как производство самосвальных платформ, были прежде всего экономические соображения. Как известно, серийный самосвал ЗИЛ-ММЗ-555, создававшийся специально для перевозки строительных грузов, в реальной эксплуатации был машиной универсальной, как и многие другие отечественные грузовики. В большом количестве самосвалы поставляли не только на строительство, но и в сельское хозяйство. Неудивительно, что корытообразный кузов малого объема, предназначенный для перевозки строительных материалов с большим удельным весом, нередко использовавшийся даже для перевозки цементного раствора, плохо подходил для транспортировки сельскохозяйственных грузов. Это вызывало недовольство руководства Минавтопрома, считавшего приоритетным производство грузовых автомобилей универсального назначения.
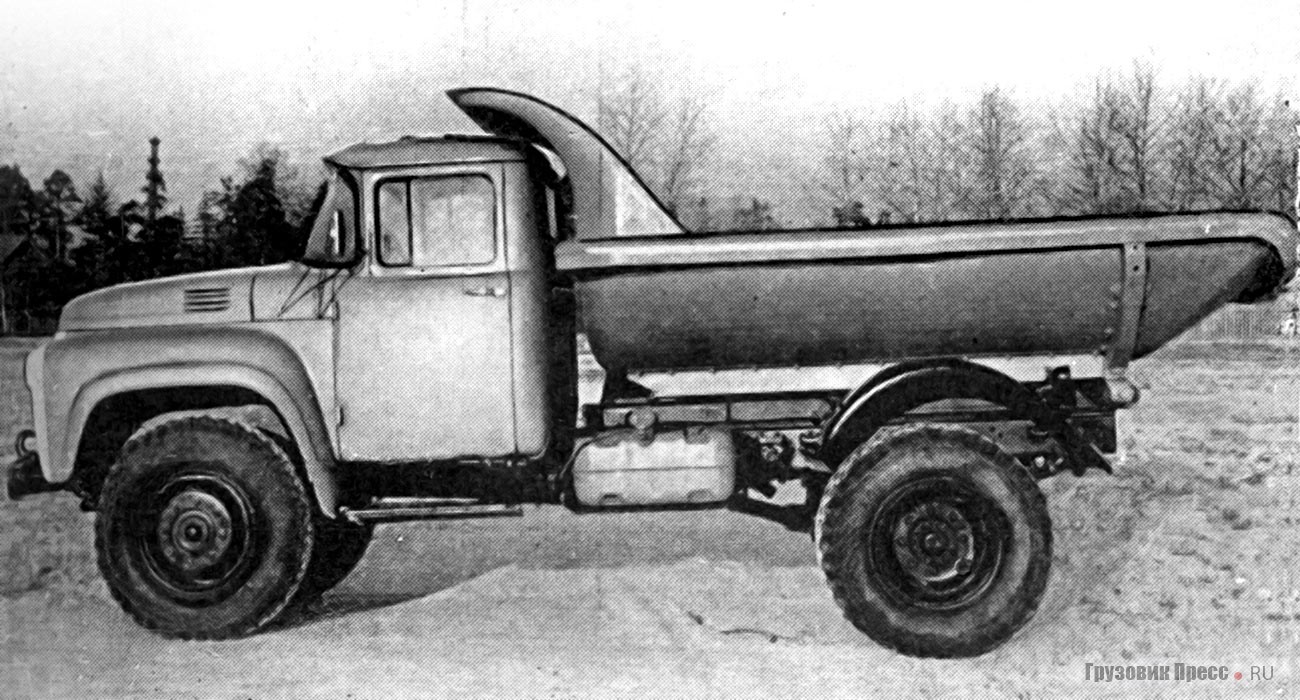
Одной из самых значимых проблем эксплуатации сельскохозяйственных самосвалов была низкая коррозионная стойкость кузова при перевозке незатаренных минеральных удобрений – вследствие химической реакции минеральных солей с металлом кузова самосвалов «сгорали» за короткое время. Стеклопластик для этих целей подходил почти идеально.
Кроме того, и в основной для самосвала ЗИЛ-ММЗ-555 области эксплуатации – строительстве – выявилась недостаточная долговечность его кузова. Эти машины нередко работали в карьере, где подвергались ударам камней, неизбежным при экскаваторной погрузке грунта, что вызывало повреждения кузова, разрушения сварных соединений. Не способствовало долговечности кузова и абразивное изнашивание днища при разгрузке сыпучих материалов, что характерно для всех строительных самосвалов. Все меры по усилению кузова могли бы привести к значительному увеличению его веса и как следствие снижению грузоподъемности самосвала, и без того недостаточной.
Еще одной проблемой, которую был призван решить стеклопластик, была трудоемкость изготовления сварных стальных кузовов. Технология изготовления кузова серийного ЗИЛ-ММЗ-555 предусматривала применение ручной дуговой электросварки, с помощью которой требовалось наложить около 40 м сварного шва. Забегая вперед, отметим, что трудоемкость не только не удалось снизить – именно технологические сложности изготовления кузовов из стеклопластика поставили крест на проекте.
Вернемся к опытному образцу. Самосвал ЗИЛ-ММЗ-555Д, как и серийный «555-й», был построен на шасси ЗИЛ-130Д1 с колесной базой 3300 мм. Пластиковый кузов самосвала представлял собой единую деталь в виде ковша без заднего борта, закрепленную на подрамнике. К кузову крепился пластмассовый защитный козырек, выполненный отдельной деталью. Вместимость кузова составляла 2,75 м3. Кузов был изготовлен на Калининском заводе пластмасс (г. Тверь) по технологии контактного формования из стеклопластика на основе полиэфирной смолы и стеклоткани. Толщина стенки кузова в наиболее подверженной ударам средней части днища составляла 15 мм, а борта имели толщину 10–12 мм.
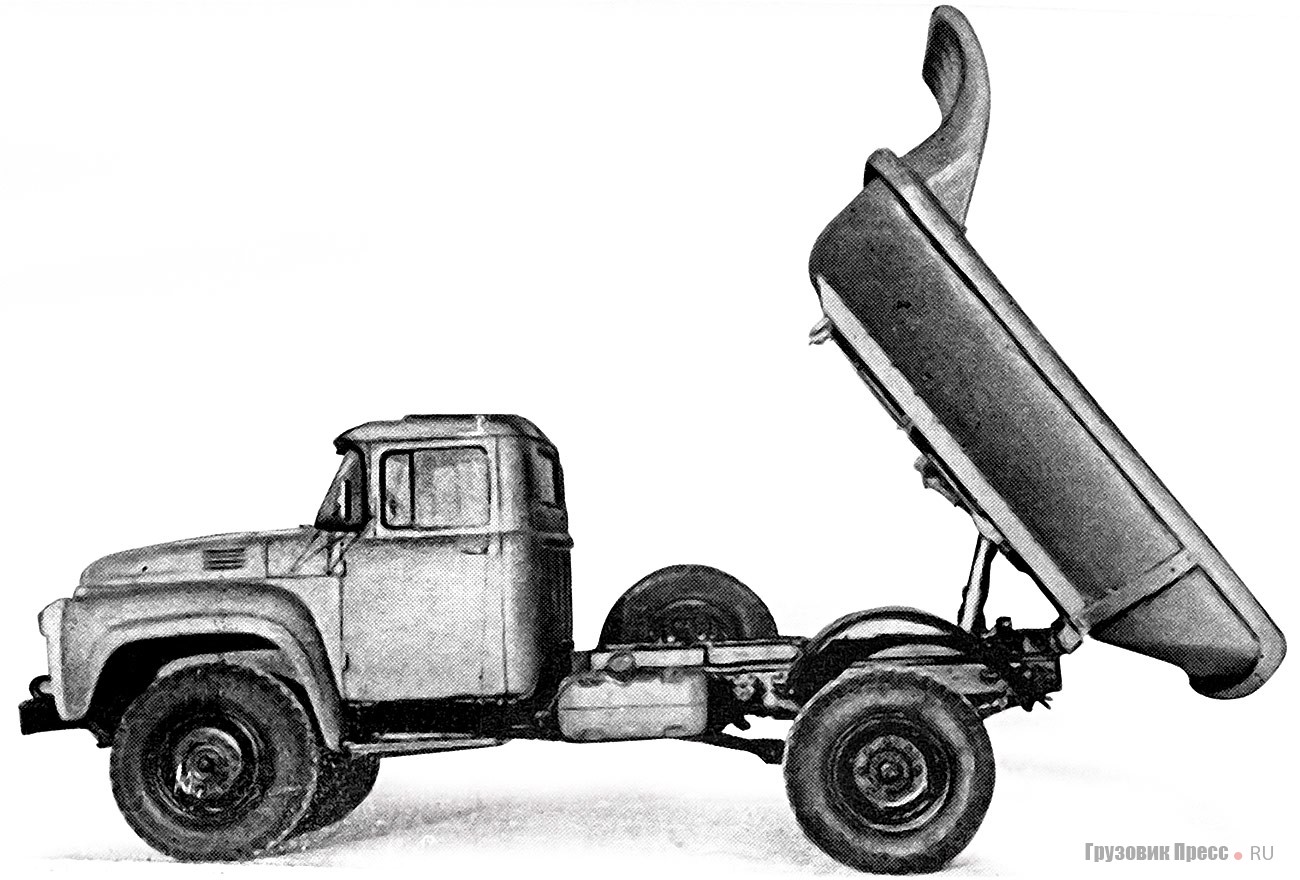
Силовым элементом кузова являлся металлический подрамник с шарнирами для опрокидывания кузова и подпятником для упора гидроцилиндра. Помимо собственно подрамника силовой каркас кузова включал единственное поперечное ребро жесткости, расположенное над поворотными шарнирами. Металлический каркас соединялся с кузовом болтами, вформованными в стеклопластик. Гидросистема опытного самосвала с телескопическим двухзвенным гидроцилиндром была полностью заимствована у ЗИЛ-ММЗ-555.
Пластмассовый кузов опытного самосвала был почти в полтора раза легче стального кузова ЗИЛ-ММЗ-555 и весил 410 кг. За счет снижения собственной массы кузова удалось повысить грузоподъемность опытного самосвала до 4,7 т, что на 200 кг превышало грузоподъемность серийного аналога.
Самосвал ЗИЛ-ММЗ-555Д был построен в единственном экземпляре и предназнался для проведения всесторонних заводских испытаний. Образец выдержал испытания весьма успешно, продемонстрировав высокую прочность стеклопластикового кузова. В заводском отчете об испытаниях самосвала особо отмечен такой факт: для проверки кузова на прочность на верхнюю кромку борта кузова из ковша экскаватора был сброшен камень массой 300 кг. При этом на кузове остался лишь небольшой задир глубиной в один слой стеклопластика.
Испытания самосвала предусматривали не менее 1000 циклов погрузки-разгрузки для оценки износостойкости кузова. Несмотря на то, что кузов неизбежно изнашивался при разгрузке грунта, особенно в задней части, результаты испытаний были признаны удовлетворительными. При этом принималась во внимание хорошая ремонтопригодность кузова – текущий ремонт заключался в проклеивании изношенных и поврежденных участков стеклотканью и не требовал специального оборудования.
Грузоподъемность, кг | 4700 |
Снаряженная масса, кг | 4300 |
Вместимость кузова геометрическая, м3 | 2,75 |
Масса кузова, кг | 410 |
Направление разгрузки | Назад |
Максимальная скорость, км/ч | 90 |
Помимо постройки опытного образца проведенные на заводе исследования предполагали и разработку технологии серийного производства самосвалов с кузовами из стеклопластика. Главным технологом завода В.В. Волковым был разработан вариант технологического процесса изготовления пластмассовых кузовов, рассчитанный на выпуск около 10 000 самосвалов в год. Для изготовления кузова, защитного козырька и брызговиков колес предполагалось изготовить специальные трехпозиционные установки, оборудованные жесткими полуформами. В отличие от традиционной технологии постепенного, послойного «выклеивания» кузова на форме (мастер-модели), применяющейся в мелкосерийном и опытном производстве, разработанная на ММЗ специально для крупносерийного выпуска технология предусматривала одновременную закладку в полуформу требуемого количества слоев стеклоткани, предварительно пропитанной смолой. Для ускорения полимеризации смолы предусматривался обогрев полуформ до температуры 50–70 °С. По расчетам производительность одной установки должна была составлять не менее одного кузова в час, а для обеспечения запланированного годового выпуска требовалось три комплекта таких установок.
Эксплуатация самосвала со стеклопластиковым кузовом при организации его серийного выпуска, по расчетам экономистов, сулила значительный экономический эффект прежде всего за счет снижения собственного веса и соответствующего повышения грузоподъемности.
Однако технологические сложности не позволили начать производство этого автомобиля. Причиной тому была значительная доля ручного труда в производственном процессе, в связи с чем трудоемкость изготовления стеклопластикового кузова не только явилась ничуть не меньшей, чем сварного кузова ЗИЛ-ММЗ-555, а значительно ее превышала. Так, например, укладка стеклоткани в полуформу должна была производиться вручную, и на этот процесс отводилось 1,5–2 часа. Вероятно, при соответствующем уровне автоматизации производства можно было достичь требуемого объема выпуска, но вполне естественно, что мытищинские технологи ориентировались на производственные возможности завода, и на появление автоматических линий тогда рассчитывать не приходилось. В итоге к крупносерийному производству стеклопластиковых кузовов, которое, безусловно, требует автоматизации технологического процесса, автомобилестроение в то время оказалось не готово.
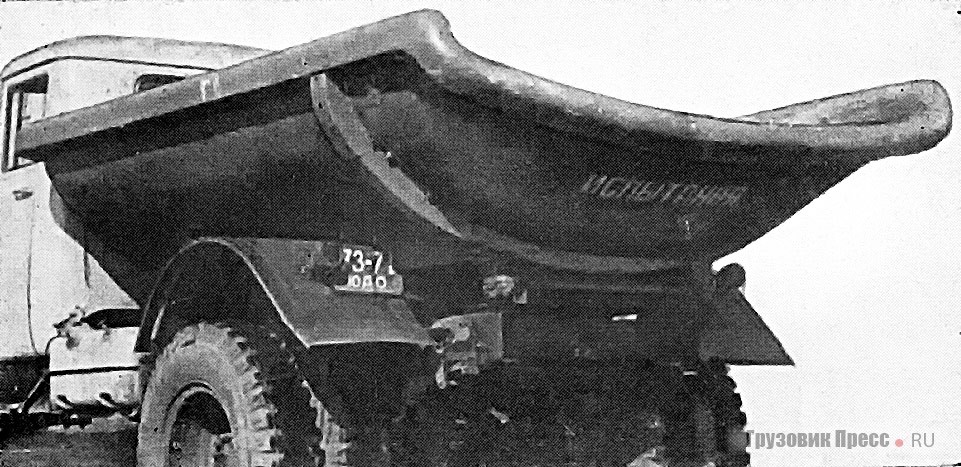
Тем не менее главная цель исследований была достигнута – подтвердилась пригодность стеклопластика в качестве основного конструкционного материала для платформ строительных самосвалов. И несмотря на то, что с тех пор серийные самосвалы с пластмассовыми кузовами не появились, тема использования пластика в самосвалостроении вновь обрела актуальность в наши дни. В последнее время стали применяться различные полимерные составы, которые наносятся на внутреннюю поверхность стальных самосвальных платформ для их защиты от изнашивания и коррозии.
На самом Мытищинском машиностроительном заводе применение пластмасс в опытном производстве велось достаточно долго. В 1974 г. был разработан и испытан стеклопластиковый козырек для самосвала ЗИЛ-ММЗ-555, рекомендованный к производству. В 1973–1974 гг. испытывались пластиковые брызговики колес для самосвалов ЗИЛ-ММЗ-555 и ЗИЛ-ММЗ-554. Был построен даже опытный образец легкового прицепа ММЗ-81021 с кузовом из стеклопластика. Но это уже другая история.